Guía Calibración Impresoras 3D SLA/Resina
Manual en impresión en resina para iniciarse.
En esta guía vamos a intentar ayudar en esos primeros pasos con este tipo de impresoras así como dar alguna información que también pueda ser de ayuda a aquellos que ya tengan una impresora y quieran sacarles el máximo potencial.
Si queréis podéis entrar en las comunidades de Telegram, en español, donde podréis encontrar más información y ayuda de otros compañeros:
Por otro lado si podéis encontrar review de impresoras de resina de las principales marcas donde se os facilitará descripción de la máquina, primeros pasos y algunos tips que pueden ser útiles:
Anycubic
Uniformation
Que es la impresión 3D en resina?
Probablemente algunos de vosotros vengáis de impresoras de filamento (FDM) donde se utiliza un filamento el cual fundimos para crear capa a capa nuestras figuras. En las impresoras de resina, aunque el objetivo final es el mismo que es crear una figura 3D, utilizamos una resina fotocurable para crear capa a capa nuestras piezas.

Tenemos diferentes tecnologías de impresión 3D en resina como SLA/DLP/MSLA las más populares y con diferentes combinaciones.

Este tipo de impresoras utilizan un tanque donde tenemos una resina fotocurable, básicamente que esta se solidifica cuando es expuesta a radiación UV. La parte mecánica de la impresora baja la plataforma de impresión hasta una altura, altura de capa de impresión, y de esa forma capa a capa se van curando y formando nuestras piezas creando un modelo 3D.
En el caso de las impresoras SLA, Stereolithography Laser Apparating, se utiliza un láser y va curando los diferentes puntos que forman las diferentes capas.
En DLP, Digital Light Processing, disponemos de un proyector UV que cura la capa entera en una vez por capa.
En MSLA, se utiliza una pantalla LCD que actua de máscara para dejar o no pasar los UV de una fuente.
El proceso tal como os indicamos es similar entre todas esta tecnologias, la plataforma va bajando y subiendo para hacer cada una de las capas hasta que nuestra pieza se forma.
Partes de una impresora 3D de resina
A continuación os vamos a describir brevemente las partes de una impresora de resina, utilizaremos de ejemplo una Anycubic M5s Pro aunque todas básicamente tienen las mismas partes.

Cúpula o campana protectora (Removable Cover), básicamente permite cerrar el área de impresión para evitar que los UV afecten a la resina, manipular la máquina durante la impresión y contener los gases producidos durante esta. Dependiendo de la marca/modelo puede ser como la de la foto, o abatible o estilo puerta.
Eje Z (Z Axis), es el brazo donde se monta la cinemática de la impresora... guia/s lineal/es, anclaje de la plataforma de impresion, varilla y motor. Es una parte fundamental ya que de la robustez de su construcción va a depender la precisión de cada capa.
Plataforma de impresión (Build Platform), es la plataforma donde se van adhiriendo nuestras capas para formar la figura final. Construida en aluminio normalmente suelen llevar un grabado láser para mejorar la adherencia de capas.
VAT o tanque de resina (Resin VAT), es el depósito donde pondremos la resina. Este depósito normalmente suele ser de aluminio y en ocasiones con un tratamiento anti adherente. En el fondo de este VAT nos encontramos con un film transparente y flexible del cual os hablaremos más adelante.
Protector de pantalla (Protection Film), suele ser aconsejable cuando nuestra impresora no lo lleva instalado de serie el poner un film que proteja la pantalla ante filtrados de resina o incluso de pequeños golpes por restos de resina. Lo ideal es utilizar cristales templados H9 finos y sin polarizar, aunque también podemos utilizar acetatos que aguanten temperatura. Las propias marcas o terceros ya suelen vender este tipo de protectores.
Pantalla LCD (Exposure Screen), tal como vimos en el punto anterior es una pantalla que va a permitir el paso o no de los UV. Estas pantallas tienen un tiempo de vida limitado, se consideran consumibles, además que filtrado de resina o golpes pueden dañarla relativamente fácil.
Fuente UV (Light Source), al igual que el anterior ya vimos al inicio de la guía el uso de la fuente UV. Es importante recalcar en esta su potencia y su sistema óptico para que llegue de forma homogénea a todo el área de impresión. Además dado que genera bastante calor es siempre importante mantener una buena ventilación para alargar su vida útil.
Panel/Pantalla de control (Control Panel), es la pantalla desde donde vamos a poder acceder al interfaz de control de la impresora... siendo a día de hoy la inmensa mayoría táctil.
Fuente de datos (Data Input), la forma en la que daremos acceso a nuestra impresora a los ficheros laminados. Normalmente tenemos conexiones USB y en impresoras más modernas o de más alta gama interfaces de conexión a red o WiFi.
Accesorios, dependiendo del modelo nos podemos encontrar con:
Sistemas de filtrado o extracción de gases/vapores, siempre aconsejamos los sistemas de extracción con filtro pero algunas marcas/modelos incluyen un pequeño sistema de filtrado carbon activo que poco más que eliminan el olor de la resina además de requerir cambiar ese carbono a menudo porque se saturan rápidamente.
Sistemas de calefacción, muy importantes en este tipo de impresoras disponer de ellos en especial si nuestra impresora está en sitios con bajas temperaturas o corrientes de aire. Ya os explicaremos más adelante la importancia de la temperatura.
Sistemas de llenado automático de resina, también suele ser muy útil en especial en impresoras de gran volumen para asegurar que no nos quedamos sin resina o por seguridad a la hora de manipular la resina.
Resinas 3D
Como ya hemos visto una parte fundamental de esta tecnología de impresión es el uso de resinas que mediante el proceso explicado se solidifican formando nuestras piezas.
Entre las propiedades de las resinas podemos ver algunas como alta resolución, transparencia, flexibilidad, velocidad de impresión, etc.
La elección de la resina es un aspecto crucial porque va a afectar el acabado y propiedades de nuestras piezas así como requerir determinados ajustes, máquinas o procesos para utilizarlas.
Resinas Estándar, suelen ser la solución más económicas y usadas normalmente además de compatibles con el 90% de las impresoras. Tienen una buena precisión y definición que las hacen ideales para un uso general aunque pueden ser no tan adecuadas para impresiones de alta velocidad o bajo determinadas temperaturas de trabajo, producir un alto grado de olor en ocasiones y normalmente estas se limpian con detergentes químicos como IPA.
Resinas lavables al agua, unas resinas muy populares entre la gente y que fueron una "invención" de los fabricantes para hacer más "segura" y "sencilla" la impresión en resina... la realidad es muy diferente. Son unas resinas que en lugar de usar detergentes químicos utilizan agua para realizar la limpieza... si, suena genial!!! Pero tal como veremos más adelante este agua se ha de tratar correctamente y se han de tener las mismas medidas de seguridad que con cualquier resto del proceso que tenga restos de resina... vamos que no se puede tirar el agua por el desgue. Además estas resinas normalmente suelen ser más débiles tendiendo a "estallar" o partirse ya sea durante el post-procesado... o incluso a los días/semanas/meses si no tenemos cuidado.
Resinas lavables al agua... que tener en cuenta con ellas para evitar problemas?
Como ya os hemos comentado estas resinas tienen mucho marketing detrás y lleva a los usuarios a tener determinadas expectativas que después no son todo lo buenas y maravillosas.
En este caso no nos vamos a centrar en el tema de seguridad y tratamiento de residuos si no en que aspectos tener en cuenta para evitar que nuestras piezas se partan con facilidad:
Proceso de curado, tal como os comentábamos estas resinas tienden a ser algo delicadas y el proceso de curado durante la impresión y especialmente en el post-procesado pueden agravar esto. Intenta siempre ajustar correctamente los tiempos de curado durante la impresión. Intenta ajustar los tiempos de curado durante el post-procesado, haz pruebas siempre, cura durante periodos de tiempos cortos cambiando de posición las piezas... por ejemplo si la pieza requiere 3m de curado haz un curado de 1.5m en una posición, cambia la posición y cura el mismo tiempo y vuelve a realizar el proceso. Evita dejar tus piezas expuesta a la luz directa solar durante periodos grandes de tiempo.
Secado, este tipo de resina tiende a absorver humedad lo cual por sus características puede iniciar procesos químicos que rompan la estructura de nuestras piezas. Es más que aconsejable que después de la limpieza de la pieza sequemos muy muy bien las piezas especialmente por zonas poco accesibles... podemos utilizar aire comprimido, un secador o pistola de calor idealmente también para que con un poco de calor ayude al secado. Deja las piezas durante minutos/horas antes de proceder al curado, asi aseguras que el secado es óptimo. Nunca realizar el curado si las piezas están húmedas!!!
Mezclado de resina, para mejorar este tipo de resina y evitar algunos de estos problemas suele ser una buena idea mezclar alrededor de un 10% de resina flexible (o hacer pruebas hasta encontrar el % adecuado en tu caso) .
Almacenaje de nuestras piezas... Evita almacenar las piezas en lugares con alta humedad o calor. Idealmente en lugares secos y con temperatura ligeramente baja. Aplicar una capa de sellante, como barnices acrílicos con protección UV, pueden ayudar a proteger la absorción de humedad.
Resinas ABS, son unas resinas que contienen partes de ABS (Acrylonitrile Butadiene Styrene) que básicamente es un polimero termoplastico que tiene una buena resistencia y dureza excelente para piezas mecánicas o que queramos un extra de dureza y resistencia a golpes.
Resinas Flexibles, probablemente por el propio nombre ya te haces una idea de su función. Su principal característica es que nuestros objetos podrán ser mas o menos flexibles. Estas resinas suelen ser compatibles con la mayoría de impresoras pero es importante tener en cuenta que para un correcto uso se han de realizar unos buenos ajustes en las opciones de impresión como tiempos de exposición, velocidades, tiempos de descanso, distancias, etc...
Resinas Alta Temperatura, de nuevo son unas resinas muy enfocadas a usos concretos... en este caso a soportar temperaturas altas que eviten degradaciones o pérdidas estructurales de integridad en nuestras piezas. Principalemente pensadas para el uso en piezas mecánicas en entornos con condiciones especiales.
Resinas Técnicas, disponemos de otros tipos de resinas técnicas como castables para fundido, con base a materiales como Nylon, etc...
Seguridad
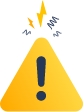
La resina y otros matEstándarue usaremos durante el proceso pueden ser peligrosos si no se manipulan correctamente... POR FAVOR TOMA TODAS LAS MEDIDAS DE SEGURIDAD!!!
La resina y otros productos químicos que usaremos son o pueden ser altamente tóxicos y peligrosos ya que provocan aerosoles tóxicos que pueden causar problemas de intoxicación realmente serios.
En el caso de sentirnos mareados, a punto de desmayarnos o tener dolores de cabeza... SALIR DE LA HABITACIÓN INMEDIATAMENTE!!! al aire libre si es posible y no entrar en la habitación hasta sentirnos mejor entrando momentaneamente a abrir ventanas o activar purificadores de aire para ventilar/limpiar bien la habitación, hasta que eso suceda mantenerse fuera.
Algunos fabricantes venden sus resinas o productos indicando que son más o menos tóxicas, la realidad es que ante la falta de certificados oficiales y su dudosa procedencia el consejo es manipular cualquier producto químico con la mayor precaución posible.
Por otro lado y además de generar aerosoles tóxicos que podemos inhalar los componentes que manejamos durante la impresión 3D también es dañina para la piel, puede provocar irritaciones y reacciones alérgicas por lo que es imprescindible el uso de guantes de goma de silicona o nitrilo.
En el caso que entremos en contacto con resina líquina hay que limpiar la zona urgentemente con agua tibia, ya que el agua fría puede reaccionar con la resina y volverlas pegajosas y difíciles de retirar, y aplicando antes jabón en la zona.
En la siguiente tabla podéis ver algunos de los componentes que son usados en las formulaciones de las resinas 3D y sus aspectos nocivos para la salud:

Algunos mitos que nos gustaría que tengáis claro con la seguridad y que son importantes a modo resumen:
La resina lavable al agua es una solución más sergura que las normales.
FALSO!!!
Estas resinas tienen una composición igual o peor en ocasiones que las resinas normales. La diferencia es que su fórmula permite el uso de agua para su limpieza, para lo bueno y lo malo. El agua es un detergente menos tóxico que el IPA, pero, por otro lado, se han de tratar y desechar esa agua de forma correcta al ser tóxica, además de que su reutilización es menor comparada con IPA. Además, este tipo de resina suele ser menos rígida y puede dar problemas con el tiempo al rajarse si no se cura muy bien interna/externamente.
La resina de menos olor o Bio son menos tóxica.
FALSO!!!
La falta de olor no necesariamente está relacionada con que sus vapores no sean tóxicos. De hecho, algunas formulaciones de resina para evitar olores usan compuestos que pueden llegar a ser más tóxicos incluso que la resina normal. Lo mejor para el tema olores es priorizar una ventilación de extracción, filtros de carbono/HEPA y ventilación constante del área de trabajo. Con respecto a las resinas Bio es similar, el hecho de ser fabricadas con componentes bio no significa que no sea tóxica y es importante comprobar el MSDS (datasheet de seguridad)
Ponerse guantes es opcional.
FALSO!!!
Los guantes, a ser posible de nitrilo, son una barrera para que la resina no toque nuestra piel. Si no manejamos correctamente la resina esta puede tocar nuestra piel pudiendo producir diversas reacciones adversas como quemaduras o alergias.
La resina curada es segura al tacto y contacto con comida.
FALSO!!!
Las piezas curadas pueden contener residuos o restos de resina que pueden ser dañinos al contacto con la piel tal como vimos en el punto anterior.
Filtros de carbono filtran todas la toxicidad de la resina.
FALSO!!!
Los filtros de carbono son relativamente efectivos en la reducción de olores y determinador VoCs (partículas suspendidas) pero no todas. Además este tipo de filtros se saturan muy rápidamente y se han de reemplazar los filtros a menudo para que sean efectivos. Lo mejor es priorizar una ventilación de extracción, filtros de carbono/HEPA y ventilación constante del área de trabajo.
Usar mascarillas de tela son suficientes para la impresión en resina.
FALSO!!!
Este tipo de mascarillas, las típicas que encontramos en los propios kits de las impresoras, son totalmente insuficientes para filtrar VoCs emitidos durante la manipulación/proceso de impresión en resina.
En el siguiente video de nuestro compañero VogMan podéis encontrar mucha información sobre estos temas interesante:
Medidas de protección
A nivel básico os aconsejamos:
un entorno bien ventilado de forma continua, esto ayudará a diluir los contaminantes en suspensión reduciendo su exposición
extracción y filtrado del átrea de impresión, el uso de sistema de extracción al exterior y/o el filtrado activo mediante equipos con filtros HEPA/Carbono van a permitir reducir significativamente los contaminantes
disponer de áreas reservadas para impresión, que delimiten el acceso a personas que puedan manipular o usar indevidamente los materiales relacionados con impresión
utilizar el correcto equipamiento de protección, como guantes... gafas de protección... sistemas de ventilación ABEK
En la siguiente imagen podéis ver, con respecto a los diferentes pasos o procesos de impresión en resina, cuando es obligatorio el uso de uno o varios sistemas de protección:

Tal como hemos comentado hay que tener cuidado trabajando/manipulando impresión en resina por lo que os aconsejamos usar estos componentes de protección:
Máscara de respiración con cartuchos de filtro de alta calidad. En nuestras impresoras suelen venir unas mascarillas téxtil que NO protegen.
Es aconsejable comprar siempre máscara y cartuchos de filtrado originales, esta en juego tu salud!!!
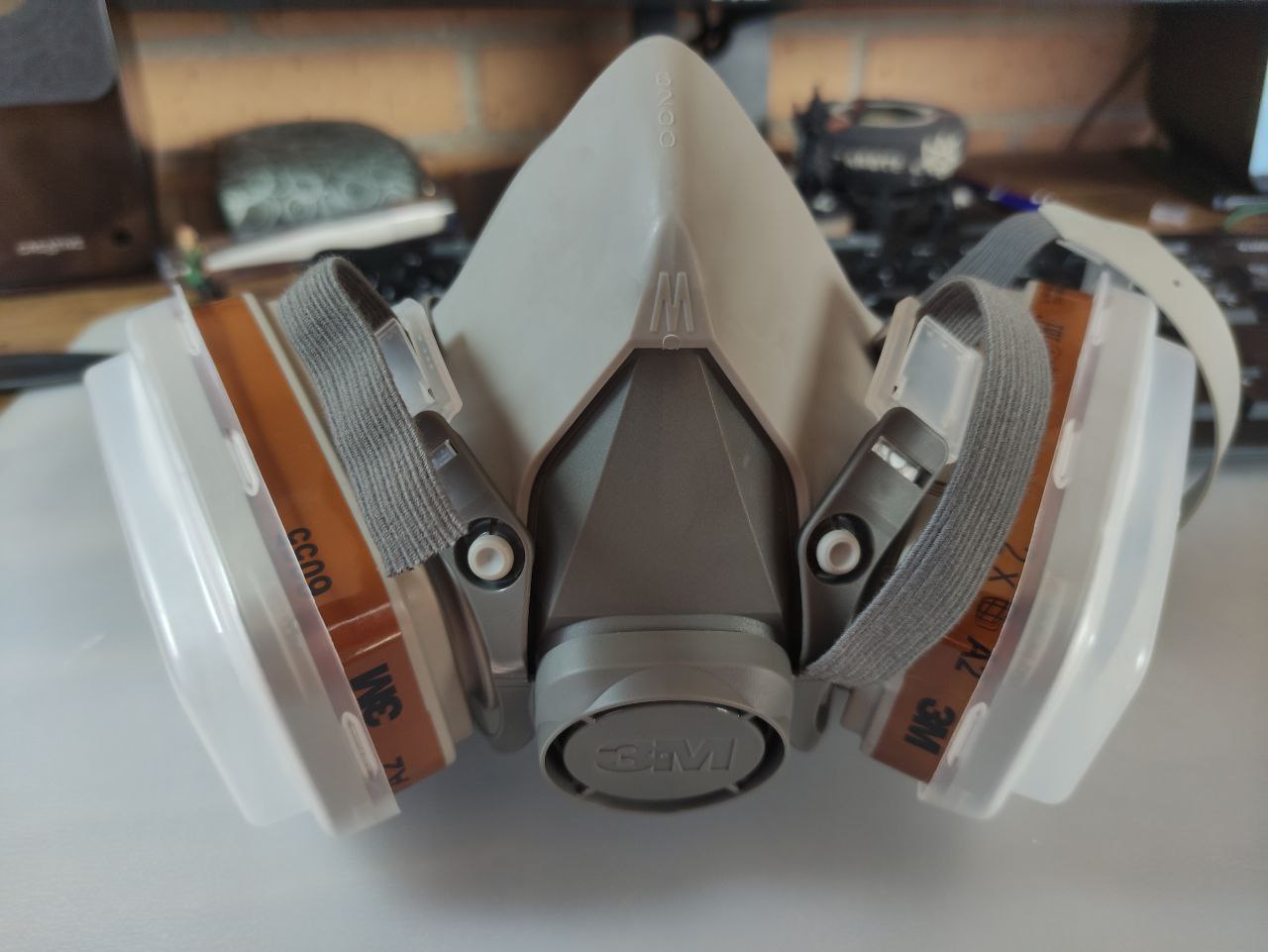
Gafas protectoras, como ya hemos comentado la resina puede provocar irritación e incluso alergia por lo que es más que aconsejable protegernos con unas gafas de cualquier salpicadura o traza de resina sólida durante el proceso de manipulación de la pieza.
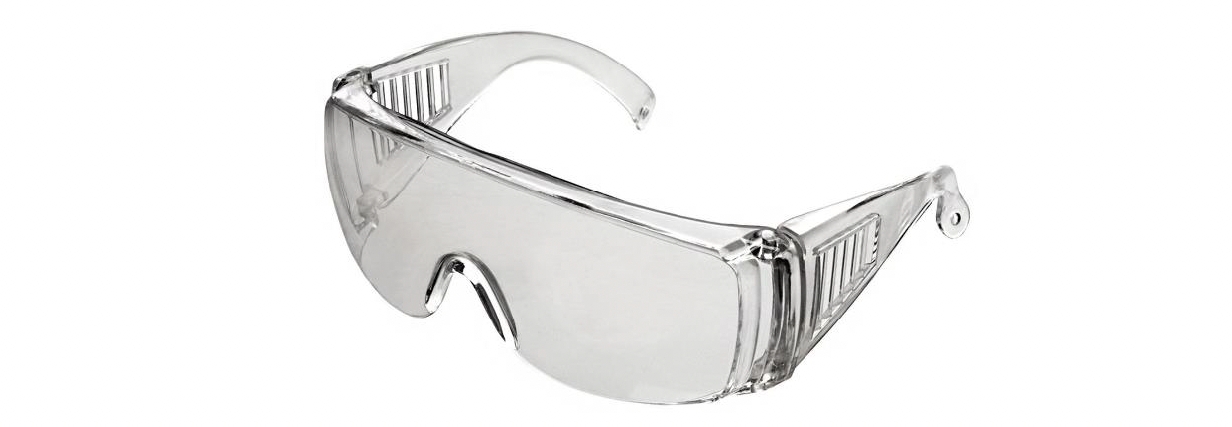
Guantes de silicona o nitrilo, para evitar el contacto con los productos químicos que manipularemos
Filtros de aire, en este aspecto indicar que pese a que algunas impresoras llevan filtros estos son normalmente de carbono que se centran más en reducir el olor que no en proteger de los aerosoles tóxicos.
Es aconsejable disponer de un purificador de calidad en la habción donde tengamos nuestras máquinas y/o un extractor hacia el exterior además de asegurarnos que se encuentren en un lugar bien ventilado o que podamos ventilar fácilmente.
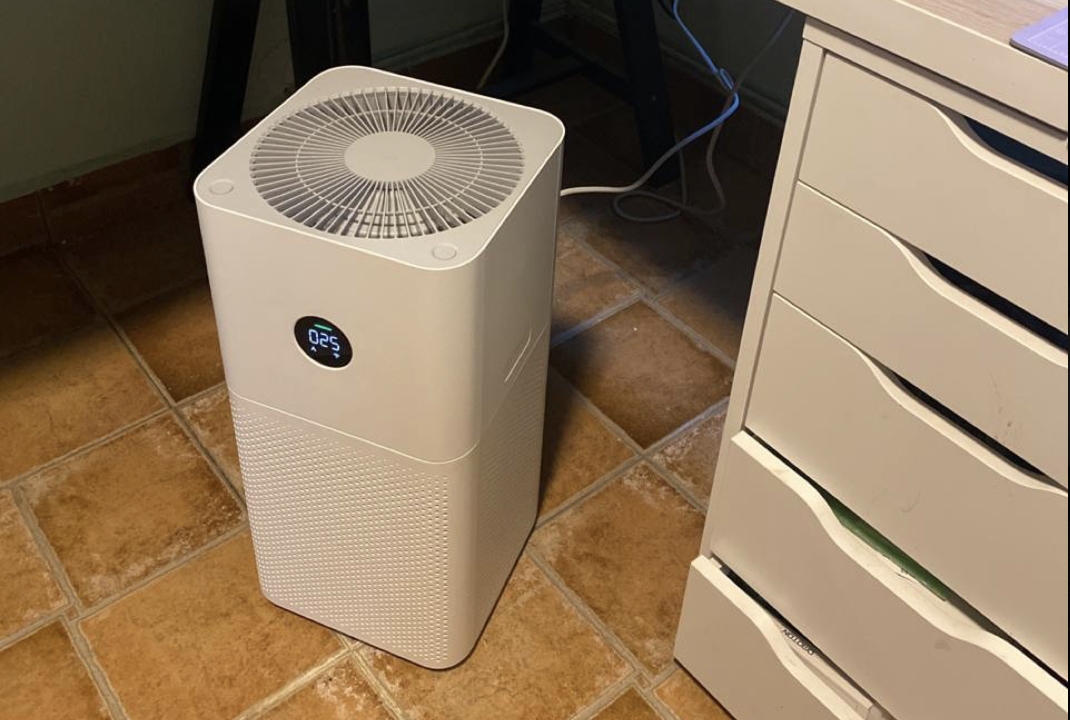
Tapa, idealmente de silicona, para nuestro VAT. Esto evitará por un lado que la luz UV natural pueda llegar a la resina y por otro lado contener los vapores/aerosoles cuando no estemos usando el VAT y lo tengamos con resina.
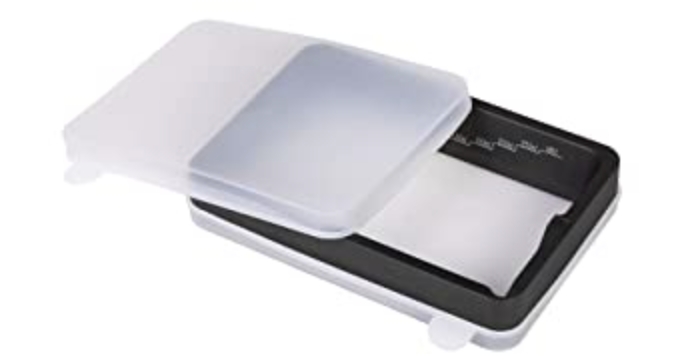
Herramientas
La impresión en resina require de una mayor manipulación de nuestras piezas así como de nuestras máquinas por lo que es imprescindible asegurarse que tenemos disponible las herramientas adecuadas que necesitemos durante el proceso:
Caja para almacenar todas las herramientas e utensilios, a ser posible plástica y en negro para que no atraviese la luz.
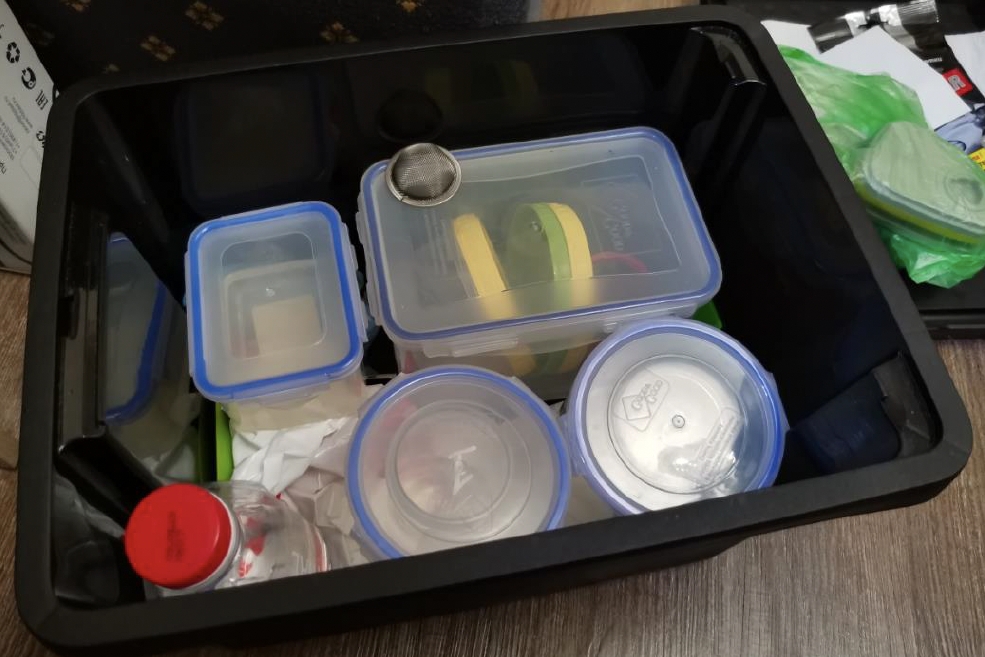
3 tuppers plasticos con dimensiones suficientes para el volumen de impresión de nuestra impresora que usaremos para el pre-lavado, lavado y proceso de filtrado/limpieza el IPA.
En el caso que tengamos una máquina de lavado/curado, algo muy aconsejable por la comodidad y seguridad que aporta al proceso, es aconsejable disponer de una segunda cubeta para el pre-lavado y en este caso un tercer tupper para el filtrado/limpieza el IPA.
Filtro/colador resina, todo y que suelen venir algunos con la propia impresora tener un colador de té va fenomenal para el filtrado de la resina.
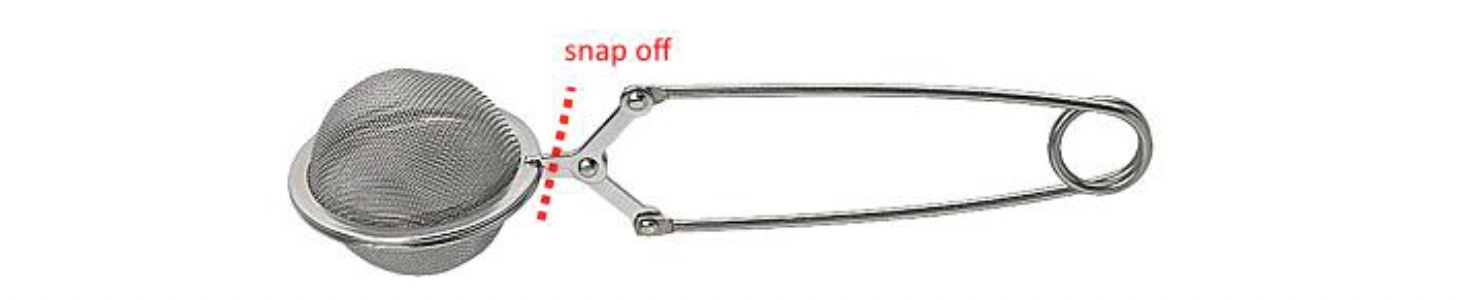
Espátula de silicona, como las usadas en cocina ya que son muy útiles para remover la resina en el VAT y evitar dañarlo.
Toallitas IPA o trapo microfibras, para limpiar con IPA los utensilios
Pinzas a ser de plástico para recoger cualquier resto que encontremos en el VAT
Una jeringa de gran capacidad va sensacional para poder vaciar el VAT de resina de una forma cómoda y segura -
Máquina de curado y lavado, aunque podemos fabricarnos una caja de curado y realizar el proceso de lavado a mano, es más aconsejable y suele dar mejores resultados hacerse con una máquina de este tipo.
Manipulación de la impresora
Normas básicas
NO intentes quitar la resina con agua fría ya que como hemos comentado la resina cuando entra en contacto con agua fría se vuelve muy pegajosa y viscosas.
Usa toallitas o trapo microfibras con IPA o en su defecto agua tibia con jabón. En resinas lavables al agua usaremos agua tibia con jabón sin problema)
Es importante colocar nuestra impresora en una superficie plana y estable para que no tengamos problemas con nuestro nivel de resina durante la impresión.
También es aconsejable que se encuentre en una zona protegida ante menores o mascotas así como bien ventilada.
Nunca toquemos el FEP con nada que no sea goma blanda o silicona.
Puedes dejar la resina en el VAT durante mucho tiempo, no le pasará nada a tu FEP por ello. Tan solo asegurate que esta tapado el VAT para evitar luz UV y emisión de aerosoles y a ser posible tapa también tu máquina con una funda téxtil negra que evite que entre la luz.
Mezcla en el VAT o agita bien el bote de resina antes de una impresión, agita de forma circular nunca evitando movimientos de "barman" :) mezclaras de una forma uniforme y no crearás burbujas en exceso, y deja reposar unos minutos para evitar burbujas en tus impresiones.
Se recomienda que la resina se encuentre entre 25-35 grados para un resultado óptimo. Podemos hacer este proceso de diferentes formas como usar un calefactor, calentar la superficie de la plataforma de impresion con un secador, poner el bote de resina en un calienta biberones o bajo agua caliente, etc...
Utlizar siempre un colador cuando pasemos la resina del VAT al bote, incluso si la impresión/es salieron perfectas.
Revisa periódicamente el FEP, tensado, daños y aplicar una capa fina de lubricante PTFE seco tanto al FEP como al VAT alargarán la vida del mismo y el porcentaje de impresiones sin problemas.
Protección pantalla
Las nuevas impresoras, normalmente monocromáticas, no llevan protección entre la pantalla y el FEP algo que puede ser un desastre si tenemos algún accidente.
Aunque los fabricantes no suelen aconsejarlo es muy aconsejable protegerlas teniendo diferentes alternativas:
uso de acetato fino 0.2 o inferior
protector, plastico no rígido, de tablet o similar
protectores comerciales ya hechos para nuestras máquinas
La instalación dependiendo de cual usemos puede ser más o menos compleja intentando siempre cubrir la máxima zona de la impresora y evitando cualquier burbuja que pueda quedar entre el protector y la pantalla.
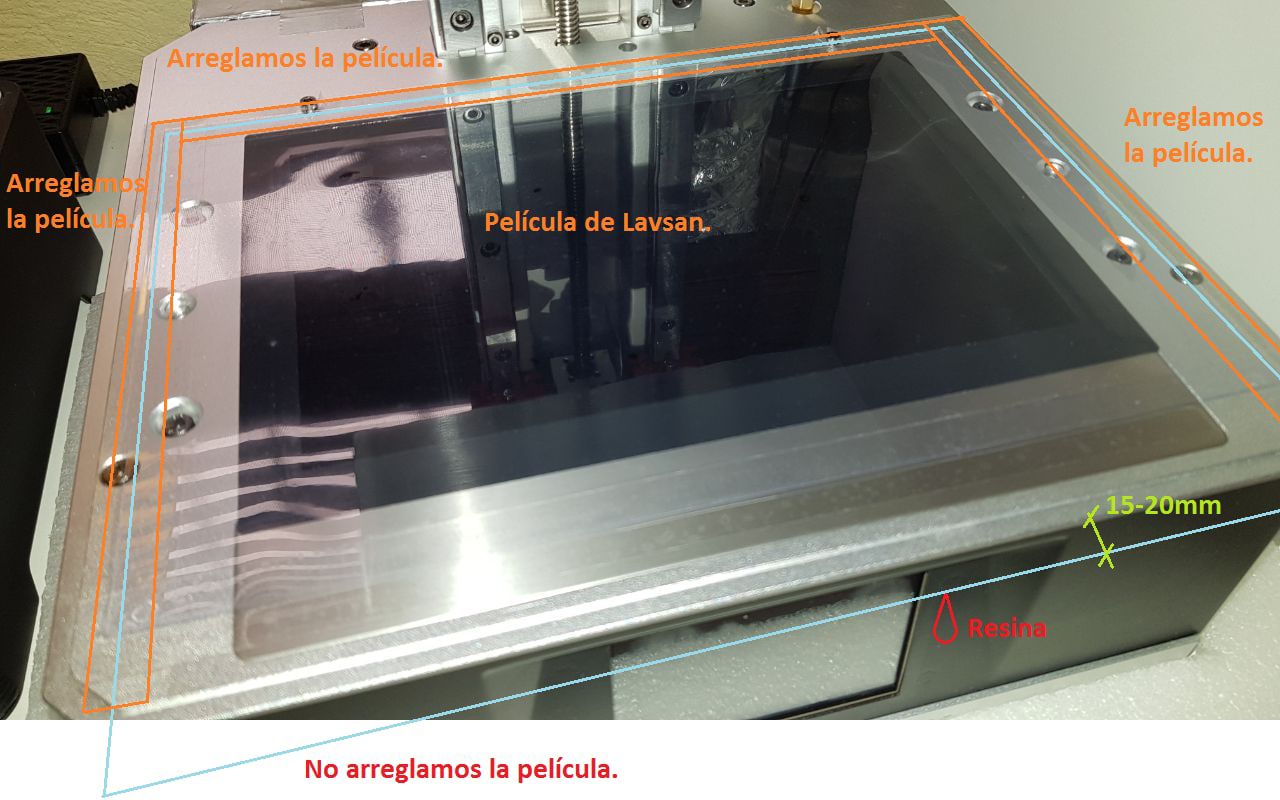
Nivelación de plataforma
El proceso de nivelación de la plataforma es uno de los más importantes para que tengamos un reducido % de fallos en nuestras impresiones.
Por el funcionamiento de las impresoras de resina nuestras piezas se adhieren a la platafoma de impresion y se van formando, al retraer la plataforma para ir creando capas se crean unas tensiones que de no tener una correcta nivelación y ajustes de tiempos en estas capas base van a afectar a la impresión.
Hay básicamente 3 métodos para nivelar, los diremos del mas sencillo al más simple:
nivelación automática, en máquinas recientes contamos con algunos modelos de impresora que se nivelan de forma automática simplificando el proceso.
nivelación manual utilizando una hoja de nivelación, suele ser el sugerido por los fabricantes y el más seguro si tenemos en cuenta daños a la máquina y sus componentes y al usuario. Normalmente el proceso es muy sencillo y explicado en las instrucciones del fabricante.
nivelación manual directamente en el VAT, otro método que suelen utilizar los usuarios avanzados es realizar el nivelado directamente sobre el VAT. Esto tiene algunas ventajas como que no necesitamos retirar el VAT o limpiar la pantalla. Por contra corremos riesgo de dañar el film del VAT, corremos más riesgo de entrar en contacto con la resina por lo que es más necesario aún contar con guantes/gafas de protección, tenemos que estar seguros que no quede ningún resto de resina o podremos dañar algo.
Rellenar resina
Retirar tanque resina (VAT)
En diferentes ocasiones vamos a necesitar retirar nuestro VAT de la impresora como por ejemplo al hacer una limpieza, sustitución del FEP, etc.
Es importante tener en cuenta que por la naturaleza de materiales y proceso de impresion el VAT puede quedar adherido a nuestra pantalla así que retirarlo de una forma incorrecta puede dañar o romper nuestra pantalla o el FEP.
Os aconsejamos seguir estos sencillos pasos:
Aflojaremos los tornillos de sujección del VAT.
Levantaremos, tal como vemos en la siguiente foto, el VAT desde la parte frontal primero para que este se despegue lentamente de la pantalla y permita la entrada de aire.
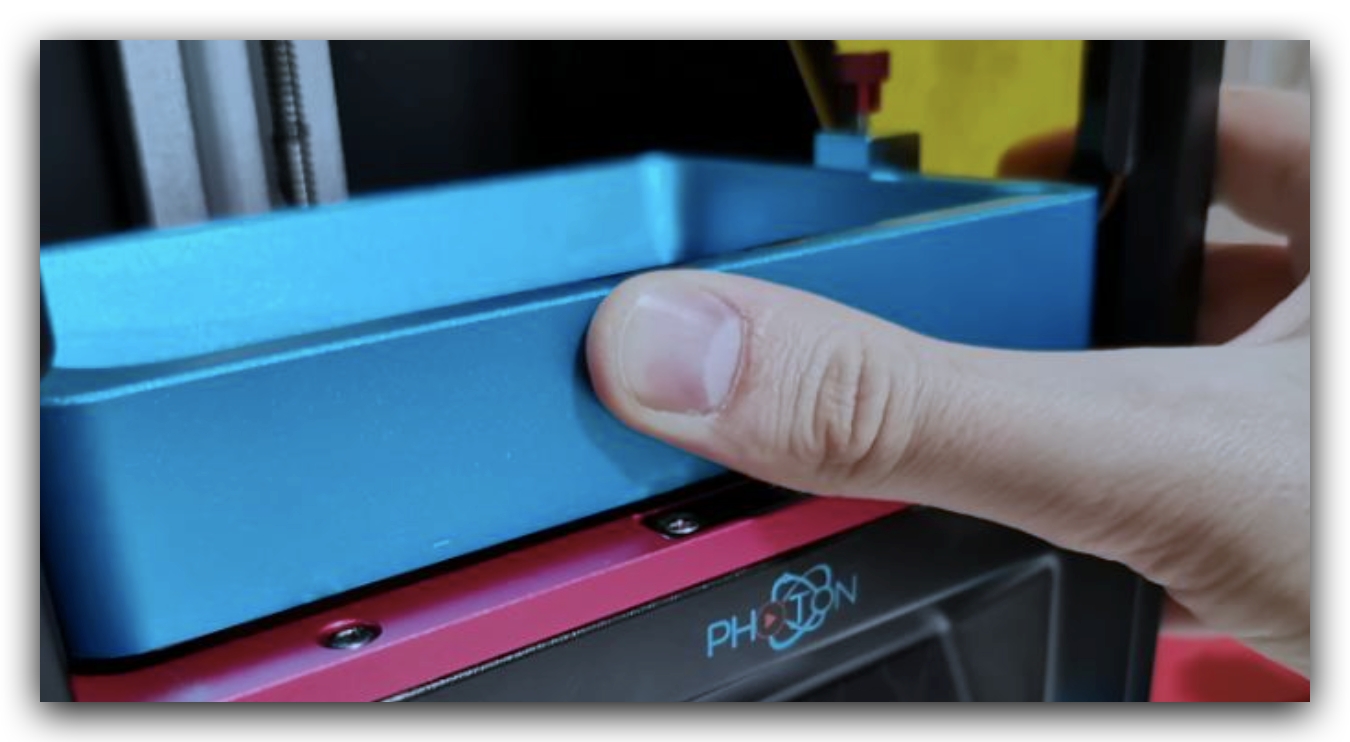
Seguiremos levantando poco a poco el VAT dentro de la ubicación original y cuando veamos que despega sin problema retiraremos el VAT de su ubicación.
Retirar resina curada en el FEP
Cuando falla una impresión esta puede quedar adherida a nuestro FEP, a continuación os sugerimos diferentes procedimientos para retirar la resina curada y que no dañe nuestro FEP.
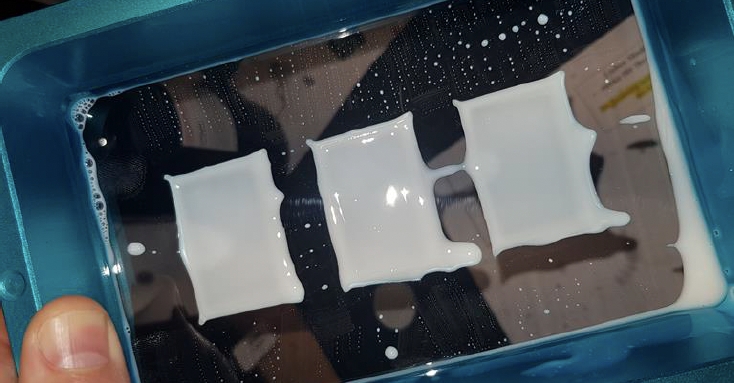
Nunca intentes retirar la resina curada del FEP con nada afilado ni que pueda cortar!!! puede provocar fugas y destruir tu pantalla u otros daños más graves.
Para nosotros la forma más sencilla para realizar el proceso es usar la funcionalidad que llevan muchas impresoras precisamente para esto o el test de UV de nuestra pantalla que suelen disponer todas.
Este proceso como podrás ver en el siguiente video básicamente lo que hace es hacer un curado de una capa muy fina que después se puede retirar de una forma muy sencilla con restos de soportes, con una pieza impresa diseñada para ello o con la misma espátula de silicona.
También podemos realizarlo de forma mas manual vaciando nuestro VAT y desde la parte inferior ir "masajeando" la resina curada en una de sus esquinas con la yema de los dedos y circularmente... al cabo de unos segundos debería de comenzar a despegarse.
Retirar resina curada en la pantalla
Aunque siempre aconsejamos el poner un protector en las pantallas de nuestras impresoras si estas no disponen de uno en ocasiones puede suceder que por cualquier accidente o impresión fallida nos caiga resina en nuestra pantalla y en el peor de los casos esta cure.
Una solución muy sencilla es usar una esponja que cubra la zona afectada y poner sobre ella agua caliente 60-70 grados con un poco de IPA durante unos 15m, una vez pasados estos 15 minutos procederemos a quitar con cuidado la esponja y con una espátula plástica retiraremos con mucho cuidado la resina de la pantalla.
A continuación tenéis un vídeo del proceso.
Sustituir film (ACF,nFEP/PFA,FEP)
El film se suele calificar como un consumible por lo que es aconsejable revisarlo periódicamente para asegurar que no esta dañado o tiene fugas. Las impresoras de nueva generación llevan un contador de capas que nos indica/informa cada cuanto es aconsejable cambiarlo y dependerá del tipo de film que usemos.
ACF
30K capas
nFEP/PFA
10K capas
60K capas (z-tilt)
FEP
El film permite el paso de la luz para curar nuestra resina por lo que tiene que estar siempre perfecto. En todo caso que este un poco turbio o con pequeñas abolladuras o rayas no deberían influir. Además dependiendo del tipo de film este va a comportarse de una forma u otra al paso de la luz, dependiendo de su composición y grosor, que podemos ver en la siguiente tabla a modo orientativo:

Tenemos diferentes tipos de film que son más o menos adecuados dependiendo de la máquina y uso de la misma:

Estas características van a permitir unas mayores o menores velocidades y distancias a la hora de imprimir. A modo de ejemplo:

A continuación tenéis una tabla resumen:
PROS
Baja tensión de adherencia, facilita impresión de alta velocidad
Reduce el riesgo de fallos de impresión
Se pueden lograr velocidades de impresión altas junto con una resina y máquina adecuada
Mayor durabilidad
Media tensión de adherencia, facilita impresión a velocidad
Excelente transferencia de luz
Coste medio
Excelente transferencia de luz
Coste menor
CONS
Actualmente, tiene un coste algo superior
Durabilidad media
Alta tensión de adherencia, dificulta impresión de alta velocidad
Baja durabilidad
Características
Grosor 300µm
Pérdida intensidad paso de la luz aprox. -7%
Grosor 127µm
Pérdida intensidad paso de la luz aprox. -5
Grosor entre 50-150µm
Pérdida intensidad paso de la luz aprox. entre -1.5-5.4%
En resumen, si buscamos un film que priorice la durabilidad y aprovechar la velocidad de las maquinas actuales así como un extra de durabilidad ACF suele ser el más apropiado. Si queremos priorizar coste y una mayor transmisión de luz que puede resultar en mejores detalles en máquinas con resoluciones XY medias o bajas sin importarnos el tiempo de impresión o durabilidad del film podemos utilizar FEP/nFEP.
Deberemos sustituir el film cuando este tenga abolladuras profundas, marcas o rayas que generen artefactos en las impresiones, también en el caso que veamos separación de capas en el fip (es u rasguño que tiene una telaraña que se extiende desde él) y que suelen indicar una rotura inminente... o por último que no genere la tensión suficiente para el proceso de curado.
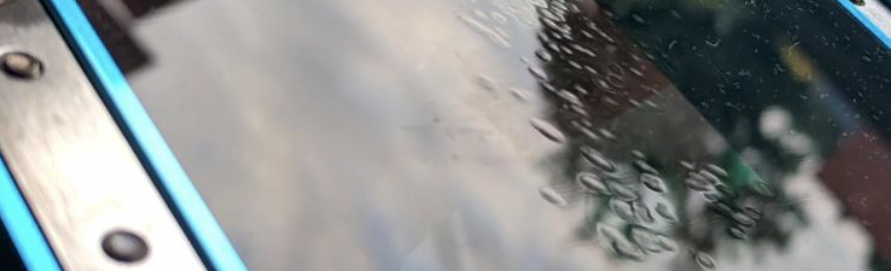
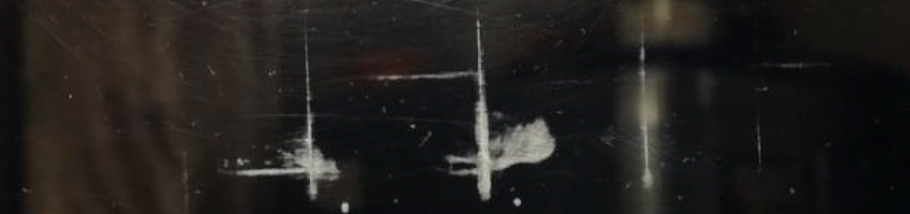
El proceso de sustitución del film es sencillo y adjuntamos algunos videos útiles, en cualquier caso y dependiendo del sistema que use nuestra máquina los pasos serían:
Retirar el antiguo film
Retiraremos toda la resina del VAT/tanque
Utilizaremos IPA de al menos 95% pureza para limpiar el VAT/tanque con un microfibras o similar que no deje residuos o produzca arañazos, especialmente en la zona de los anclajes de los tornillos
Retiraremos todos los tornillos de la parte inferior del VAT, los cuales dejaremos en un recipiente con IPA para ser limpiados cuidadosamente, que sujetan la estructura del film
Extraeremos la estructura que sujeta el film
Retiraremos el resto de tornillos para poder extraer el film antiguo, estos tornillos también los limpiaremos con IPA cuidadosamente
Instalación del nuevo film
Con IPA limpiaremos muy bien toda la estructura del VAT especialmente he la hendidura donde se anclan todos los tornillos
Colocaremos el nuevo film entre las dos partes de la estructura donde retiramos el anterior, es importante realizar este proceso sobre una superficie limpia y plana pondremos la primera parte de la estructura, colocaremos el film nuevo encima y colocaremos la segunda parte de la estructura. ACF, recuerda que la parte mate de este tipo de film ha de quedar en la parte interna del VAT en contacto con la resina.
Os aconsejamos utilizar la propia plataforma, completamente limpia, para fijar en la posición correcta todo el conjunto como podéis ver en la siguiente imágen
Otro tip interesante es usar una plantilla que permita mantener una tensióón uniforme durante la instalación: https://www.youtube.com/watch?v=9YY5MNZw_6w
Utilizaremos la propia llave Allen para perforar el film en los agujeros de anclaje de la estructura
Comenzaremos a poner los tornillos iniciales comenzando por las esquinas diagonalmente
Una vez tenemos las 4 diagonales haremos las partes centrales como vemos en la siguiente imagen
Instalar el nuevo film en el VAT/tanque
Ahora que ya tenemos el nuevo film en su estructura con todos los tornillos de anclaje procederemos a montarlo en el VAT/tanque y colocaremos los tornillos de anclaje siguiendo el mismo proceso que hicimos antes... empezaremos por sus diagonales y después las centrales
Nos aseguraremos que todos los tornillos esten apretados firmemente
Cortaremos el exceso sobrante del film con cuidado de no dañar nada
Deberemos asegurarnos una buena tensión del FEP que realice un sonido como si fuera un tambor :D
Con respecto a la tensión del FEP tenemos diferentes "trucos" para ver que este correcto:
El primero que ya os indicamos en uno de los pasos anteriores es que la instalación del film se realice con este tensado de una forma homogenea, esto permitirá que el tensado sea uniforme.
Utilizar una aplicación de análisis de frecuencia sonoras para analizar el sonido que hace al tacto. Tenemos aplicaciones como Sound Spectrum Analyzer (iOS) o Spectroid (Android) que nos van a indicar esta frecuencia entre 275-350Hz... no es una ciencia cierta y depende de las diagonales de nuestra impresoras... donde suelen funcionar correctamente tienes un video de ejemplo del proceso -> https://www.youtube.com/watch?v=Yr_wtZqBfbQ&t=837s
Algunos modelos podemos encontrar unas herramientas para imprimir que ayudan con la tensión de instalación correcta, usar tapones de refresco o incluso un número de cartas de juegos de mesa :)
Os adjuntamos algunas video guías específicas para algunas marcas:
Photon、PhotonS、Photon Mono SE、Photon Mono M5
Photon X、Photon Mono X、Photon Mono X 6K、Photon Mono X2、
Photon M3、Photon M3 Plus、Photon M3 Max、Photon M3 Premium、Photon Mono X 6Ks
Photon Zero、Photon Mono、Photon Mono 4K、Photon Ultra、Photon D2、Photon Mono 2
Photon Mono M5s
Preparando nuestras impresiones
Laminado de nuestras piezas
Si eres nuevo en el mundo de la impresión de resina probablemente no tengas claro como puedes hacer que tu impresora, a partir de un modelo 3D, pueda imprimir.
Las impresoras no saben interpretar un objeto 3D de forma directa, es ahí donde entran en juego los "laminadores" o "slicers". Estas aplicaciones lo que hacen es interpretar un objeto 3D y "procesarlo" creando un fichero con el formato adecuado para que nuestra impresora lo pueda imprimir.
Tenemos diferentes laminadores en el mercado la mayoría son gratuitos o de subscripción que nos permiten tener más avanzadas herramientas para mejorar el laminado y el acabado final de nuestras piezas en algunos casos.
Nosotros vamos a centrarnos básicamente en los dos más populares, Lychee y Chitubox... otros laminadores van a ser muy similares en uso a estos dos.
Lychee es un software de laminado relativamente reciente que dispone de un interfaz y flujo de trabajo muy intuitivo además de opciones avanzadas muy interesantes.
Dispone de versión gratuíta y de pago, siendo esta última la que cuenta con ciertas mejoras para mejorar el laminado. Podéis encontrar más información aquí.
Ponerlo en marcha es muy sencillo una vez instalado:
Añadiremos el perfil de nuestra máquina del listado de máquinas soportadas

Añadiremos nuestros objetos 3D

Ajustes de pieza, Layaut, desde aqui colocaremos y angularemos nuestras piezas a nuestro gusto

Prepararemos nuestra pieza, Prepare, donde colocaremos soportes, haremos el ahuecado y drenajes, etc...

Por último laminaremos nuestra pieza, Export, al formato adecuado que utilice nuestra máquina

Tips para el laminado de piezas
Soportes
Suele ser un problema muy común en usuarios nuevos que las piezas fallen quedándose en el film de nuestro VAT dejando solamente los soportes y su base... algo que puede ser frustrante, un gasto de tiempo y resina además de un riesgo ya que podemos dañar nuestro film o incluso algo más serio.

Básicmente necesitamos soportes por varias razones, relacionadas con la propio tecnología de impresión:
voladizos, no podemos imprimir al aire por lo que necesitamos disponer de soportes que puedan mantener estos voladizos o puentes.
adhesión, para mejorar la adhesión ya que no podemos normalmente ni es aconsejable imprimir directamente a la base de impresion nuestras figuras utilizamos los soportes para anclar nuestras piezas a la base
soporte, aunque parezca obvio los usamos para permitir un mejor soporte y que las fuerzas que se realizan durante la impresión no afecten o muevan nuestras figuras haciendo que estas se deformen significativamente y pierdan sus dimensiones originales

Identificar que tipo de soporte necesitamos, nos basaremos en 3 premisas:
Soportes para fijar nuestras piezas, usaremos soportes gruesos colocados normalmente en la parte más bajo de la pieza y en zonas donde no sea visible o sencilla de reparar. Estos soportes van a permitir un buen anclaje de la figura a nuestra base de impresión para dar robustez.
Soportes de ayuda ala fijado, normalmente del tipo medio y colocados en zonas que veamos que pueden soportar cierta tensión durante la impresión y sirvan de ayuda extra a la fijación y crecimiento de la pieza
Soportes para detalles o islas, en este caso usaremos soportes pequeños ya que su función será la de soportar áreas pequeñas sin mucha tensión durante la impresión.
Una forma simple de entender lo anterior seria pensar en nuestras piezas como un árbol, en la parte baja tenermos un tronco grande y fuerte para soportar toda la estructura, en la parte media buenas ramas para aguantar el resto del árbol y por último las pequeñas ramas finas para soportar hojas.

Algunos parámetros a tener en cuenta a la hora de configurar nuestros soportes:
diámetro en puntas de soporte, normalmente se aconseja utilizar puntas finas en los soportes entre 0.2-0.5 y estos pueden variar dependiendo de la zona que tengamos que soportar. Recuerda que diámetro como la penetración van a afectar en las posibles marcas que estos puedan dejar una vez retirados.

densidad de soportes, nos va a ayudar a mejorar aquellas zonas que necesiten un mayor aporte de estabilidad y evitar artefactos durante la impresión. Una buena angulación como explicaremos más adelante pueden reducir el uso de estos

altura de elevación, esta es la distancia que se elevará la pieza con respecto a la base... se recomienda un valor de entre 3-5 mm normalmente
interconexión de pilares, este tipo o función en los soportes permite crear una estructura interconectada de estos que permite disponer de unos soportes más robustos reduciendo el riesgo de fallos.
Algunos problemas o sugerencias relacionadas con los soportes:
Las piezas se separan de los soportes, para evitar un uso excesivo de soportes que tienen un impacto en resina o en el tamaño de los mismos para reducir las marcas en las piezas en ocasiones estos pueden ser insuficientes con respecto a la pieza y podemos compensar:
aumentando el diámetro de la punta o área de contacto, va a dejar unas marcas más pronunciadas pero menor riesgo de que la pieza se separe de los soportes
incrementar la densidad de soportes, usar un diámetro de punta menor pero incrementar la cantidad o densidad de soportes para compensar
correcto uso de las herramientas de tu laminador, los laminadores de hoy en día tienen opciones de crear soportes de forma automática que nos pueden servir de base para ajustarlo según nuestra necesidad, experiencia y tipo de pieza... aunque tengan esta función nunca olvides revisarlos y ajustarlos!!!
velocidades de impresión importantes, en especial aquellas que controlan el "despegue" de la pieza de nuestro film del VAT... si usamos velocidades altas estas tensiones pueden ser muy grandes y debemos tener unos buenos soportes
el estado y tipo del film del VAT importa, el film del VAT (FEP/nFEP/PFA/ACF) es muy importante ya que va a permitir que los soportes soporten más o menos tensiones. Films como PFA o ACF reducen mucho la adhesión al film y por lo tanto crearan menos tensiones a tener que aguantar por parte de los soportes. De la misma forma el estado y tensión de este van a afectar.
Ángulación de nuestras piezas al laminar
Utilizar un ángulo óptimo al laminar nuestras piezas nos va a favorecer en:
reducir el tiempo de impresión
normalmente reducir la superficie impresa reduciendo de esa forma la temida tensión o succión provocada por el movimiento del eje Z y el FEP
asegurarnos unas superfícies bien definidas y sin artefactos

A continuación tenéis una calculadora con la que poder calcular el ángulo óptimo para vuestra impresora:
Ahuecado, ancho del perímetro y agujeros de drenaje
Dependiendo de la sección de nuestro/s objetos a la hora de imprimir puede ser aconsejable el ahuecado de estos.

El ahuecado va a permitirnos:
un menor gasto en resina
normalmente reducir la superficie impresa reduciendo de esa forma la temida tensión o succión provocada por el movimiento del eje Z y el FEP
Con respecto al grosor del perímetrto o muro al realizar ahuecados este va a depender del tipo de pieza o acabado final de estas en cuanto a resistencia. Normalmente valores entre 1-4mm suelen ser los más usados recomendando 1mm para objetos pequeños e ir añadiendo grosor a medida que nuestras piezas sean más grandes o requieran de una mayor resistencia.
Es importante recordar que cuando usamos ahuecado de piezas hemos de colocar agujeros de drenaje. El tamaño y ubicación van a depender de la pieza pero es aconsejable tener al menos dos drenajes uno en la parte superior de la pieza y otro en la parte inferior.

Corrección de tiempo estimado de impresión
Los laminadores intentan calcular el tiempo de impresión en base a los parámetros que el controla en base al modelo de impresora, en ocasiones no dispone de todos los datos para hacer un cálculo exacto (verdaderamente siempre va a ser aproximado entre un 10-20%).
En la mayoría de los laminadores actuales contamos con opciones para corrección/ajuste de las desviaciones de estimaciones de tiempo:
Desde Lychee disponemos de un método sencillo para permitir una estimación de tiempos más exacta.

Dentro de nuestra configuración de resina veremos una sección para ajustar los tiempos de impresión (1) la habilitaremos.
En Time per Burn in layer (2) pondremos los tiempos que midamos en nuestra impresora al realizar las capas base... nosotros normalmente medimos el tiempo del total de capas base + transición (Burn In Layers - Number of Layers + Transition Layer Count) y dividimos por el número de estas el tiempo resultante que será el valor a poner.
En el caso de Time per layer (3) realizamos el mismo proceso midiento el tiempo de 5 capas normales y dividiento el tiempo total que nos de entre 5 y lo colocamos ahí.
Con estos ajustes Lychee calculará de una forma bastante más exacta, dependiendo de impresora/perfil, que el que da por defecto.
Calibración/Ajustes finos laminador
Calibrar correctamente el tiempo de exposición es un factor crítico para asegurarnos que nuestras piezas se impriman sin problemas y con la máxima calidad.
IMPORTANTE!!!
Los valores, aún en máquinas iguales, puede variar por múltiples factores así que lo ideal partas de una base de configuración que disponga tu laminador para tu máquina y mediante tests encuentres tus valores óptimos
Estos valores obtenidos pueden variar dependiendo de las condiciones de impresión, por ejemplo en verano podemos encontrar que necesitamos unos tiempos menores de exposición óptimos comparados con invierno por culpa de la temperatura ambiente.
Las resinas tienen diferentes formulaciones lo que también puede afectar a nuestras configuraciones/ajustes
Utilizar diferentes alturas de capa va a impactar significativamente en nuestras configuraciones/ajustes por lo que es más que aconsejable obtener nuestros valores óptimos también dependiendo de la altura de capa.
Antes de comenzar a explicar otros conceptos me gustaría explicar cuales son los 3 tipos de capas que utilizan las impresoras de resina:

Capas base o primeras capas, son las primeras capas que va a realizar nuestra impresora y son críticas para la correcta adhesion de nuestras figuras a la plataforma de impresión. Aspectos importantes que veremos más tarde son el número de estas y sus tiempos de exposición.
Capas de transición, en ocasiones son más importantes de lo que pensamos, básicamente estas capas adaptan el tiempo de exposición de las capas base a las capas normales para que no se produzcal el efecto llamado delaminación o que las capas no se adhieran entre ellas.

Por último tenemos las capas normales que son las que se encargan de los soportes y el propio objeto a imprimir. En este caso es importante un ajuste fino de los tiempos de exposición para obtener unas capas bien adheridas y con el máximo detalle posible.
Ajustes básicos
Principalmente, existen otros valores un poco más avanzados que no os aconsejamos modificar inicialmente, contamos con cuatro configuraciones/valores muy importantes a tener en cuenta:
Tiempo de exposición de primeras capas (burn-in layers exposure time, bottom exposure time, initial exposure time, base layers exposure dependiendo del laminador). Estas primeras capas son críticas dado que van a soportar la tensión de nuestra pieza y sus soportes al realizar el proceso de impresión. En este aspecto es importante:
Número de primeras capas (number of burn-in layers, number of bottom layers, bottom layer count, number of base layers dependiendo del laminador), un valor bajo o uno muy alto pueden ser contraproducentes. Tener un número pequeño de primeras capas puede hacer que estas no soporten, en este aspecto lo aconsejable es tener un número entre 4 y 6 capas base.
Exposición de primeras capas, también como el anterior pueden afectar a la adherencia de nuestra pieza y hacer fallar la impresión. Una exposición corta puede afectar a la adherencia mientras que una exposición alta aparte de provocar fallos similares va a reducir el tiempo de vida de nuestra pantalla. Normalmente, como siempre dependiendo de las condiciones de impresión y resina que usemos, este tiempo de exposición suele estar entre 25 y 40 segundos.
Tiempo de exposición de capas de transición (transition layer count, faded layers dependiendo del laminador), con el avance en los laminadores actuales tenemos disponible una función muy útil que algunas impresoras llevan por defecto en sus firmwares que son las capas de transición. Básicamente estas capas de transición lo que hacen es ir adaptando el tiempo de exposición entre las capas base, que suelen ser tiempos altos, y las capas normales para de esta forma evitar problema de adhesión entre capas o en ocasiones artefactos en forma de líneas. Establecer el numero de estas capas dependerá de cada caso pero un número aconsejable suele ser dividir el tiempo de exposición de primeras capas por X hasta que nos de un número cercano al tiempo usado en las capas normales. Ej.: tenemos un tiempo de capas base de 35s y de 2s en capas normales... 35s/X=2 aprox... 35/17=2.05 -> usaríamos 17 capasde transición.


Tiempo de exposición de capas normales (normal layer exposure time, exposure time, layer exposure time o layer cure time dependiendo del laminador), si las capas anteriores eran críticas para la adherencia de nuestra pieza a la placa de impresión, en este caso son importantes por aportar consistencia a la pieza según se va creando y lograr obtener una buena definición de detalles en nuestras figuras.
Altura de capa de impresión, la altura de capa va a impactar en el acabado final de la pieza además de en el tiempo de impresión. Es importante recalcar que los tests de exposición y otros ajustes antes comentados van a variar dependiendo de la altura de capa que usemos. Normalmente el estándar es imprimir a 0.05 mm de altura de capa que da un balance entre buenos resultados y tiempos de impresión comedidos. Para la impresión 3D en resina se considera que podemos trabajar con una calidad adecuada entre 0.015 y 0.1 mm de altura de capa.
Por otro lado cuando buscamos el máximo detalle podemos bajar estos a 0.03 o incluso a 0.015. Estos saltos normalmente se hacen por la distancia minima que puede moverse un eje Z de nuestra máquina que va en saltos de 0.015.
Otro aspecto importante para seleccionar nuestra altura de capa óptima es ver el tamaño de pixel de nuestra máquina y dado que lo que buscamos es la mejor definición usar un valor de altura de capa que nos permita obtener un voxel lo más cuadrado posible. Por ejemplo si nuestra máquina tiene una resolución de pixel de 29um la altura de capa óptima será de 30um (0.03).
De nuevo estos consejos son para sacar el máximo provecho de la máquina y conllevan por ejemplo el mayor tiempo de impresión, ajustes más finos en los ajustes de laminador o condiciones más optimas del entorno y materiales de impresión. Como dato os diremos que supuestamente el ojo humano no va a distinguir más de un 0.02 de altura de capa por lo que si quereis jugar con este parámetro lo normal es no bajar de 0.03. Por último también hemos de tener en cuenta la calidad y diseño del objeto a imprimir, una figura que no tenga una buena resolución en su diseño o que no tenga detalles finos probablemente no merezcal la pena usar una altura de capa baja puesto que no vamos a obtener ningún beneficio de ello.
Ajustes avanzados
Otros ajustes avanzados, os aconsejamos no tocar nada en un principio y dejarlos por defecto si acabamos de empezar en la impresión 3D en resina, en cualquier caso os damos unos consejos antes de empezar:
Asegúrate que obtienes unas buenas impresiones con solamente los ajustes básicos comentados en el apartado anterior.
No te pongas a cambiar todos los parámetros a la vez, lo ideal es ir cambiando un parámetro en cada test ya que si no será difícil el parámetro que nos mejora/empeora nuestros resultados.
Que fallen los tests es algo normal, lo importante es aprender que falla para continuar ajustando nuestra configuración para aprender los límites de nuestra máquina/resina.
Sentido común, el proceso de impresión en resina 3D es complejo ya que actúan diferentes factores que pueden afectar al resultado no hay configuraciones "mágicas". Aplicar el sentido común conociendo la máquina/resina y las opciones/ajustes disponible suele llevar al éxito.
Configuraciones avanzadas tener en cuenta para afinar nuestras impresiones al máximo:
Velocidades, distancias en movimientos y tiempo de descanso, en este caso . Dentro de los ajustes de velocidades encontramos diferentes parámetros a ajustar:
Altura de elevación (lift height), es la distancia que nuestra plataforma de impresión subirá entre curado de capas. Esta altura de elevación ha de ser la suficiente para separar nuestro objeto del film (FEP, nFEP, ACF) por lo que el tipo, elasticidad y grosor del mismo va a requerir unas distancias u otras. También va a afectar el tamaño del volumen de impresión así como la superficie de curado por capa siendo siempre aconsejable la angulación y ahuecado de nuestras figuras siempre que sea posible/viable.
Normalmente es aconsejable usar los valores del fabricante, por otro lado si cambiamos de tipo de film (FEP, nFEP, ACF) o queremos optimizar los tiempos de impresión es un valor con el que podemos obtener mejoras en este aspecto.
Velocidad de elevación (lift speed), es la velocidad que nuestra plataforma de impresión utilizará durante los movimientos de elevación. En cuanto a que valores usar... pues depende de gustos o si queremos priorizar % de impresiones no fallidas o velocidad, ni los propios fabricantes dan unas recomendaciones iguales y mientras algunos sugieren utilizar velocidades bajas otros aconsejan velodicades altas. También en según que máquinas se dispone de TSMC, que básicamente lo que hace es dividir la velocidad de elevación en dos partes... una inicial más lenta y otra más rápida. En nuestras pruebas suele ser la que mejor resultados nos ha dado teniendo un balance entre fiabilidad y velocidad. Aconsejamos comenzar con los valores por defecto y experimentar para nuestro caso.
Detalle del funcionamiento de TSMC
Velocidad de retracción (retract speed, platform lower speed), al igual que el punto anterior hace referencia a la velocidad que utilizará durante los movimientos de aproximación al FEP para el curado de una nueva capa. De nuevo aconsejamos dejar con los valores por defecto ya que normalmente no suele afectar a la calidad de impresion, aunque si que afecta a los tiempos de impresión. Un consejo es que dependiendo de la viscosidad y estado de nuestra resina ajustemos este parámetro, por ejemplo con resinas viscosas usar valores más bajos.
Tiempo de descanso después de retracción (rest time after retract, light-off delay, exposure off time, total off time, rest time before lift, rest time after lift), esta configuración nos va a permitir añadir una pausa o tiempo de descanso despues de que nuestra plataforma de impresión se encuentre en la posición de curado después de un movimiento de retracción antes de comenzar de nuevo con la exposición UV. Los valores por defecto suelen dar buenos resultados, normalmente usan entre 0 y 1s, el consejo general seria el de modificar este dependiendo de la viscosidad de nuestra resitan para asegurar que esta se asienta correctamente después del posicionamiento de la plataforma de impresión. Por otro lado el ajuste de este parámetro puede ayudar a reducir significativamente los tiempos de impresión. Es importante recalcar que determinaas impresoras usan o interpretan estos valores de forma diferente:
A modo de ejemplo podéis ver el efecto "booming" que suele ser indicativo que nuestro tiempo de descanso puede no estar ajustado correctamente. Tenéis un gran artículo sobre este efecto aqui.
Anti-aliasing, por el funcionamiento de nuestras impresoras estas dejan pasar la luz UV por pixeles para curar la resina dejando estos en "blanco" para dejar pasar la luz UV.
La función anti-aliasing permite hacer pixeles de transición en diferentes tonalidades para crear unas transiciones más suaves y mejorar el efecto "pixel" en nuestras impresiones. El uso del anti-aliasing va a permitirnos, dependiendo de nuestra máquina objeto y preferencias personales, unas impresiones más suaves con transiciones entre capas menos visibles y reduciendo las lineas pixeladas... por contra en según que impresoras no está soportado o se pueden perder detalles en determinadas partes de nuestros objetos. No hay unos valores universales para ajustar el anti-aliasing ya que este va a depender de muchos factores como que la máquina lo soporte, nuestra preferencias personales de acabado, etc... en cualquier caso os sugerimos unos parámetros que suelen funcionar en la mayoría de casos aunque también contamos con tests específicos como podremos ver más adelante:
Os sugerimos las siguientes opciones:
Anti-aliasign > Smooth Surfaces
Radius > 2px
Grey Offset > 40%
High Definition Anti-aliasign > On
Anti-aliasign on Supports > Off


Potencia UV (UV power, LED power, Light PWM, UV Light power dependiendo del laminador), en determinadas impresoras contamos con la opción de poder ajustar la potencia de los UV. Normalmente los fabricantes aconsejan valores entre 60-80%, dependiendo de la impresora y el tipo de resina utilizada, dejando valores superiores en el caso de querer imprimir a grandes velocidades o usos más específicos. El ajuste de este parámetro va a impactar en los tiempos de exposición.
Tests de exposición
Como ya hemos comentado anteriormente es muy importante encontrar el tiempo de exposición óptimo para nuestra resina, impresora y condiciones de impresión.
Disponemos de diferentes tests que nos pueden ser de ayuda:
Prevenir daños en nuestro film del VAT (FEP, nFEP, etc...)!!!
Al realizar tests de exposición donde realizamos múltiples tests iguales, y en general siempre que imprimamos varias veces un mismo modelo, se aconseja siempre que sea posible rotar 90 grados la pieza y mover unos mm de la posición inicial para evitar daños o desgastes en zonas específicas de nuestro film.
Tests exposición BÁSICOS
Son unos tests especialmente indicados para aquellos que se inician en la impresión 3D en resina. El objetivo de estos tests es el de obtener el tiempo de exposición relativamente óptimo de una forma rápida y sencilla:
Es un test que nos gusta mucho también ya que está a medio camino entre los tests básicos y detalle. Podéis descargar el test desde el siguiente link:
Una vez impreso, lavado y curado revisaremos algunas partes del mismo:
Capas de transición y pié de elefante, el número y tiempo de exposición en las capas base puede provocar el efecto llamado "pie de elefante" como el que podéis ver en la imagen siguiente. Por otro lado y en referente a las capas de transición podremos observar si se crean lineas o falta de adherencia entre las capas base y las normales.

Test de cajas, en este test quitaremos las cajas/cubos de 4mm y 6mm de sus anclajes e introduciremos la de 4mm en la de 6mm y esta en la de 8mm tal como podéis ver en la siguiente foto.
en el caso que no entre correctamente necesitaremos reducir el tiempo de exposición de capas normales
en el caso que entren con holgura tendremos que aumentar el tiempo de exposición en capas normales
Es aconsejable añadir o reducir tiempos entre tests en saltos de 0.2s y 0.1s

Precisión dimensional en objetos, con un calibre podemos medir los cubos para verificar las medias de estos:
el cubo de 6mm tiene que medir 6mm en su contorno y 4mm internamente
el cubo de 8mm ha de medir 8mm externamente y 6mm internamente

Test de pilares, nos va a permitir poder generar dos perfiles útiles dependiendo de la figura que queramos imprimir.
Función para precisión dimensional y detalle, para cuando imprimimos piezas que requieran un detalle máximo con buenos soportes y precisemos de precisión dimensional máxima. Cada caja de pilares utiliza una medida de estos lo que nos ayudará a averiguar cual puede ser el tamaño mínimo a utilizar de forma segura y confiable.
Función para impresiones que requieren unos buenos soportes, en este caso el objetivo es realizar el test aumentando la exposición si no todos los pilares aparecen

Más información aquí.
Tests de exposición AVANZADOS
Estos tests requieren de más esfuerzo a la hora de ajustar los tiempos de exposición e interpretar los resultados pero por otro lado nos van a permitir el máximo detalle en nuestras impresiones:
Desde 3Dwork hemos montado un test todo en uno con lo que, bajo nuestro punto de vista creemos que son los tests más completos para ajustar nuestra impresora de resina:

Podéis descargarlo desde, recuerda darle un me gusta y seguirnos :) :
Entre los tests incluidos:
(1) Escalones, esta parte del test nos va a permitir observar cuanto fiable son nuestras primeras capas donde tenemos un escalonado donde podremos medir el grosor desde 0.25 a 1.5 mm en saltos de 0.25 mm. Podremos utilizarlo como guía a la hora de ver que tal de bien nivelada se encuentra nuestra plataforma y el impacto de precisión dimensional en el eje Z cuando realicemos impresiones pegadas a nuestra plataforma.
(2) Pines y huecos (Photonsters Validation Matrix v2), tenemos una serie de pilares positivos y negativos.
Sobre exposición, veremos que en el plano de pilares negativos (huecos en el plano) estos están mayormente cerrados
Baja exposición, veremos que no se forman correctamente todos los pines

(3) Ángulos, mediante unas columnas anguladas veremos el comportamiento de nuestra impresora para realizar superficies planas y ver angulaciones óptimas para nuestra máquina y efecto antialiasing.

(4) Texturizado (Phrozen RP Tester), Estos tests nos van a ayudar para identificar el nivel de detalle que podemos encontrar con patrones complejos. Además, la zona con patrones sobre la semi esfera podremos ver como afecta la altura de capa y valores de antialiasing (típicos escalones que aparecen en las superficies de nuestras impresiones).
Sobre exposición, veremos poca definición en las diferentes texturas o incluso totalmente unidas
Baja exposición, alguno de los patrones no llegará a formarse correctamente al no unirse

(5) Tornillo, este test consta de dos partes... uno el cilindro con rosca a modo de tornillo y el otro su negativo que deberemos de retirar del test cortando por los 4 encajes. Este test nos va a permitir verificar las tolerancias y expansión de la resina.

(6) Allen (Mundo3D Maker Test Exposure Time Resin), básicamente consta de unas aperturas de forma/tamaño de una llave Allen de 4mm.
Si la llave entra en el agujero del centro que tiene el texto OK, esta tiene que entrar sin holguras o sin presión
Si la llave entra en el agujero con el símbolo + tendremos que aumentar el tiempo de exposición en 0.1 segundos.
Si la llave entra en el agujero con el símbolo - tendremos que disminuir el tiempo de exposición en 0.1 segundos.

(7) Verticales (Michael´s Calibration Matrix), test de que nos va a dar información muy útil al ver los límites para construir formas en plano vertical de forma fiable. Se incluyen test de patron simple, puentes, columnas diagonales.
Sobre exposición, veremos que los números de la parte superior no se leen correctamente y algunas zonas están completamente cerradas los patrones carecen de definición
Baja exposición, los puentes tienden a caer o no formarse de forma adecuada, los patrones no se cierran o las columnas diagonales no se forman correctament
(8) Conos (basado en Exposure Tester v2 de Dennys Wang), básicamente la estructura de puentes ha de salir correctamente y no descolgarse de los pilares. Os aconsejamos revisar el siguiente video para más información. Disponemos de tres tests de soportes basados en los valores por defecto usados en Chitubox: - LIGHT (base 0.8mm punta 0.3mm) - MIDDLE (base 1mm punta 0.4mm) - HEAVY (base 1mm punta 0.6mm)

(9) Óvalo antialiasing (Amder Antialiasing Test de Dennys Wang), con esta figura podremos ver que tal se comporta nuestra impresora y su configuración a la hora de realizar objetos curvos complejos. Para mejorar su acabado jugaremos con los valores de antialiasign. La altura de capa también afecta a un acabado mejor.

(10) Pilares/Soportes (basado en J3D Tech´s Boxes of Calibration), este test va a simular la construcción de soportes desde 0.1mm hasta 0.28mm (saltos 0.02mm entre ellos). Si no se forman correctamente normalmente es un indicativo de que necesitamos más exposición a unque no es imperativo que se tengan que formar todos dependiendo de la impresora y configuración.

(11) Datos, en esta zona podremos anotar:
Resina que usamos para el test
Número y tiempo de capas normales
Número y tiempo de capas base
Temperatura durante el test
Tiempo de curado

Tests de exposición ESPECÍFICOS
Son aquellos que nos van a permitir verificar y ajustar aspectos específicos como nivelación y primeras capas, angulación de objetos, antialisign, etc...:
Un referente en el mundo de la impresion 3D del que ya hemos visto un par de tests anteriormente. Además de estos podemos encontrar otros tests realemente útiles:
En este caso os recomendamos, aparte de los comentados anteriormente:
Test de Antialiasing, mediante este test podremos ver cómo se comporta nuestra impresora en zonas anguladas con detalle que pueden resaltar las capas de impresión. Una vez realizado con nuestro perfil normal podemos hacer diferentes pruebas ajustando diferentes valores en las opciones de antialiasing de nuestro laminador
Otro test muy interesante es el de estabilidad del eje Z, donde podremos comprobar la precisión y calidad de nuestra impresora con piezas de altura. Aspectos mecánicos o vibraciones por componentes externos como calentadores o filtros de aire pueden ser detectados.
Test de nivelación de plataforma, con este test que podemos colocar en cada esquina y en el centro de la plataforma podremos ver ajustes necesarios para capas base o nivelación.
Test de definición, con este test podremos ver hasta que nivel de detalle podemos llegar con nuestra maquina/resina/ajustes/condiciones de impresión.
UVtools... una herramienta imprescindible!!!
UVtools es una herramienta activamente actualizada con muchas herramientas útiles para nuestras impresoras de resina como por ejemplo, análisis de ficheros, calibración, reparar archivos, conversion entre formatos y manipulación de ficheros y configuraciones.
Podéis descargar UVtools desde el siguiente link, aunque el interfaz es poco intuitivo os vamos a guiar en los pasos para crear un test de exposición múltiple mediante el cual y con solo una impresión vamos a poder testear el rango de tiempos de exposición que deseemos ahorrando tiempo.
Os vamos a poner un ejemplo para una Elegoo Saturn 3 pero el proceso es similar en otras impresoras compatibles con exposición múltiple por capas.
El primer paso a realizar es cargar el fichero de test que se incluye en nuestro USB desde el menú File/Open, el fichero ROOK.goo que es el que buscamos lo encontraremos en la carpeta ELEGOO SATURN 3 Rock Model fro Printing Test de nuestro USB.
En la ventana de UVtools podremos ver una miniatura de la pieza en la parte superior izquierda, en la parte centrar una previsualización de lo que haría la pantalla de nuestra impresora que podremos controlar con el slicer que tenemos en la parte derecha para ir moviéndonos entre capas, etc...
El siguiente paso será abrir las herramientas de calibración para seleccionar el test de exposición. También vas a encontrar otras muchas herramientas para ajustar tu máquina pero en nuestro caso nos vamos a centrar en los tests de exposición.
En la nueva ventana que nos abrirá UVtools será donde configuraremos nuestro test de exposición múltiple. Vamos a revisar las diferentes secciones.
Common properties, dado que en el paso inicial cargamos la pieza de test del USB tendremos aquí ya todo casi preconfigurado. Hemos de prestar atención a los valores marcados en el recuadro rojo que suelen ser los que necesitaremos ajustar:
Layer height (altura de capa), normalmente suele ser 0.050 aunque os podemos decir que 0.030 es un valor que le va muy bien a nuestra Saturn 3... eso si... más tiempo de impresión y para obtener más detalle vuestros ajustes de exposición, la calidad de vuestra resina y la figura a imprimir van a ser claves para poder ver mejoras significativas.
Bottom layers (capas base), tal como explicamos antes las capas base son claves para que nuestras piezas queden bien adheridas a nuestra base de impresión. En este caso la pieza de test tiene estas optimizadas para el tamaño y tensiones que pueda generar. En nuestro caso y para impresiones más generales uséis entre 4-8 capas.
Bottom exposure (exposición capas base), al igual que el punto anterior en este caso está optimizado para esta pieza de test. Dado que no vamos a realizar un test de exposición de capas base vamos a dejar este valor en 30 segundos. En el caso que veamos que no se adhieran nuestras primeras capas, y tengamos bien nivelada nuestra base de impresión, subiremos de 5 en 5 segundos hasta encontrar el valor óptimo para vuestro caso.
Normal exposure (exposición capas normales), el verdaderamente importante para el test que vamos a hacer. Dado que es el valor de referencia mínimo lo ajustaremos en un valor bajo te aconsejaría poner un valor entre 1.5 y 2 segundos... al menos inicialmente hasta que saquemos un test inicial y veamos resultados.
Pasamos a la segunda sección donde podremos configurar las opciones de nuestro test:
Pin (positive) / holes (negative), personalmente es una opción que me gusta para poder hacer el test de pines tanto positivos como negativos en la parte derecha de la figura.
Text, en nuestro caso nos gusta modificar el texto de test por el nombre de la impresora y la resina con la que hicimos el test. También es aconsejable cambiar la escala del texto a 1.5 para que sea más visible.
Preview, en la parte de la derecha de esta sección veremos una previsualización de como quedará nuestro test.
Por último iremos a la sección interesante, la de configuración de tests múltiples:
Enable, nos permitirá habilitar las opciones para configurar nuestro test de exposición múltiple.
Maximum generations, será el número de tests que queramos hacer variando en cada uno el tiempo de exposición.
Generate exposure table, al pulsar este botón nos generará la tabla de tests (4)
Exposure table, será un resumen donde nos informará de la altura de capa, exposición primeras capas y exposición de capas normales. Será en este último valor, y para nuestro caso, en el que veremos que usando el valor que pusimos en Normal exposure (Common properties) de 1.5 segundos sumará el valor de Normal step (Multiple exposures) a cada uno de los tests que hagamos.
Una vez finalizada la configuración pulsaremos sobre Exposure time finder al final de la ventana para que genere el test!!!
Una vez generado volverá a la pantalla inicial de UVtools donde podremos ver nuestro test y con el control de la derecha podremos ir viendo el proceso que realizará nuestra impresora. Ahora solamente queda ir a File/Save as... y guardar nuestro test generado en el USB e imprimirlo!!!
IMPORTANTE!!!
Te aconsejamos que hagas un test primero lanzando el test sin VAT, ni resina ni plataforma y con un folio protegiendo la pantalla... así podrás verificar que tu impresora hace correctamente los tiempos de exposición por test.
Una vez finalizado el test asegúrate de limpiar y curar correctamente para obtener el mejor resultado
Un pequeño truco:
Aunque el test que hace UVtools da mucha información, tarda muy poco tiempo en hacerse y el gasto en resina es mínimo. Puede ser muy aconsejable realizar este test con otras figuras de test. En este caso elegimos la figura de test previamente, que tenéis arriba, la abrís en vuestro laminador y generais el laminado que usaremos en UVtools en sustitución del ROOK.goo que usamos anteriormente.
Realizaremos los pasos anteriormente explicados pero en este caso usaremos también la sección final Pattern loaded model marcando Enable... ahora usaremos una figura de test personalizada para estos tests!!!
Tal como podéis ver en la imagen anterior usamos el test de columnas minis, que aunque no es uno de nuestros favoritos para encontrar tiempos de exposición, para encontrar nuestro valor de exposición óptimo con un solo test de impresión.
Impresiones Fallidas - Troubleshooting
Este apartado nos centraremos en fallos durante la impresión, si tenéis problemas a nivel de máquina os podemos remitir a las páginas de asistencia de impresoras o grupos de Telegram:
Vamos a revisar los fallos más comunes que pueden suceder con nuestras impresiones.
Os aconsejamos este "cheat sheet" de core-electronics muy visual que nos puede ser de gran utilidad:
No se imprime nada y no quedan residuos en el VAT

En ocasiones podemos encontrarnos que mandamos una impresión y no hay nada en nuestra plataforma de impresión ni en el VAT. Os sugerimos revisar:
Verificar la pantalla, retiraremos el VAT y plataforma de impresión y lanzaremos un test de pantalla que normalmente llevan las impresoras. En el caso que no disponga, con el VAT y la plataforma retirada protegiendo la pantalla con un folio, lanzaremos una impresion de test. Revisaremos que la imagen se muestre correctamente y que la potencia de los UV sea la correcta. Si vemos que la pantalla o los UV tienen problemas, revisar en este último caso si nuestra impresora cuenta con ajuste de potencia UV y que no este correcto, es probable que sea necesario reemplazarlos.
Verificar el USB, es aconsejable no utilizar los USB que suelen venir con las impresoras pero independientemente de esto si tenemos el fallo descrito intentaremos usar otro USB. Recuerda que normalmente las impresoras soportan USB en formato FAT32 con particiones de entre 8-16GB y USB 2.0.
Verificar el estado de la resina, si lo anterior nos ha funcionado correctamente otra fuente de fallo puede ser el estado de la resina. Para verificar esto podemos exponer unas gotas de resina al sol o una linterna UV durante unos segundos para ver si se solidifica.
Impresión se queda en el VAT/tanque de resina, no se adhiere a la plataforma

Un fallo bastante común es la falta de adheshión en primeras capas que pueden hacer que nuestra impresión quede en el FEP o parcialmente colgando afectando al acabado de la pieza:

Nivelación incorrecta de nuestra plataforma de impresión, realizar esta de nuevo siguiendo las instrucciones de nuestro fabricante. Si vemos que siempre nos fallan en un lado o esquina también suele ser un indicativo de una mala nivelación.

Plataforma de impresión dañada o defectuosa, en ocasiones podemos encontrarnos que la plataforma no esta totalmente plana. Con la ayuda de una regla, confiable, y una luz podemos verificar el correcto estado de nuestra plataforma

Falta de adherencia en la plataforma de impresión, hoy en día las plataformas de impresión llevan patrones grabados a láser para mejorar la adhesion. En caso de no tenerlos podemos rasgar un poco con un estropajo tipo nanas la superficie. Es también aconsejable que limpiemos bien con IPA la superficie entre impresiones.
Temperatura, como ya hemos comentado la temperatura y condiciones de impresión son muy importantes por lo que aseguraos que la temperatura de la resina sea >20º por lo menos.
Ajustar la exposición de primeras capas subiendo esta entre 2 y 5 segundos para verificar si mejora, normalmente el tiempo de estas suele ser entre 6-10 veces el valor de las capas normales. Es importante recalcar que el tiempo y número de estas primeras capas pueden reducir de forma significativa la vida útil de la parte óptica.
En otras ocasiones y por la propia tensión del proceso de impresión los soportes y bases pueden ceder, en estos casos
podemos revisar el FEP que este bien tensado y en buenas condiciones
podemos aplicar a nuestro FEP una capa de lubricante PTFE para reducir las tensiones
podemos revisar el laminado aspectos como angulación de pieza, ahuecado, agujeros de drenaje colocados correctamente...
ajustar las velocidades de elevación y retracción por debajo de 40mm/min o mediante tests ir probando velocidades inferiores en rangos de 5mm/min para las capas base
ajustar el delay light-off para nuestra maquina tenéis una calculadora con tiempos aconsejables aquí.
ULTIMO RECURSO O TRUCOS DE ABUELA!!!
En ocasiones si hemos probado todo lo anterior o tenemos prisa por ver si podemos hacer que algo se pegue en nuestra plataforma os vamos a sugerir algunas opciones que suelen funcionar con máquinas rebeldes aunque no siempre sea lo más óptimo.
Aumentar el número y tiempo de exposición de capas base y ajustar el numero de capas de transición:
número de capas base a prueba de tanques, aplicaremos la siguiente fórmula que es número_capas_base = altura_capa / altura_patin_raft... por ejemplo para una altura de capa de 0.05 mm y un patin de 1-5 mm.. 1 / 0.05 = 30 capas base. Y si, no es lo ideal porque las capas base tienen un tiempo de exposición alto degradando y reduciendo la vida de los UV y de la pantalla... por contra suele ser una estrategia que suele funcionar correctamente en situaciones con impresoras rebeldes aunque lo normal suele ser que a partir de la capa 2-3 no suela afectar a la adherencia salvo en casos complejos donde varias cosas pueden afectar al funcionamiento normal.
tiempo de capas base, en este caso aumentaremos en 10s el tiempo que tengamos y lo iremos ampliando en caso de que continuemos con problemas... hasta un máximo de 80s en pantallas monocromo ya que si no se adhiere a partir de esos valores algo más complejo puede ser el problema
capas de transición, para aplicar una fórmula sencilla de recordar y en estos casos podemos optar por dos alternativas... la primera, poner el mismo número que las capas base... segunda, no usar capas de transición que aunque es algo que no suele ser aconsejable puede compensar el desgaste por el aumento del número de capas base.
Ajuste de las distancias de retracción: dependiendo de la máquina, su estado, ajustes de velocidad o gestión automática que muchas implementan en ocasiones puede ser aconsejable aumentar estas distancias al menos 2 mm para evitar problemas y tendremos dos estrategias dependiendo de si la máquina o ajustes de laminador usan TSMC o no :
Si usamos TSMC, os aconsejamos buscar en esta misma guía que es TSMC, tendremos los movimiento para capas base y normales (dependiendo del laminador pueden o no disponer de diferentes ajustes) con valores diferentes para cada paso del TSMC... en estos casos lo ideal es añadir 1 mm al valor que tengamos en el valor de cada paso distribuyendo los 2 mm entre ambos
Si no utilizamos TSMC, directamente añadiremos esos 2 mm a los valores de retracciones que tengamos
De nuevo... estos ajustes especiales solamente son aconsejables si tenemos una máquina rebelde y que con lo sugerido anteriormente no somos capaces de obtener impresiones que se adhieran a nuestra plataforma.
Recuerda SIEMPRE en estos casos revisar que tu cubeta o VAT de resina no tenga restos de resina en el que puedan dañar tu impresora.
Puedes utilizar una espátula o, si tu pantalla cuenta con ello, la opción de limpieza de VAT o test de pantalla para poder retirar una capa fina en toda la superficie de una forma sencilla y asegurando que no queda ningún rastro.
Revisa el apartado "retirar resina curada en el FEP" de esta propia guía para información más detallada.
Las capas base no se adhieren a las normales

Aunque no suele ser un fallo muy común en ocasiones podemos observar que nuestras capas base no se adhieren a las capas normales, como por ejemplo las siguientes imagenes:


Este tipo de problema normalmente se origina por el cambio brusco de tiempo de exposición entre las capas base y las normales o porque estas últimas usan un tiempo muy bajo de exposición.

En estos casos es importante tener en cuenta:
asegurarnos que nuestras capas base están entre 6 y 10
activar las capas de transición, normalmente pondremos el mismo número que el de capas base

ajustar las velocidades de elevación y retracción por debajo de 40mm/min o mediante tests ir probando velocidades inferiores en rangos de 5mm/min para las capas base
incrementando el tiempo de exposición de las capas normales un 20%
ajustar el delay light-off para nuestra maquina tenéis una calculadora con tiempos aconsejables aquí
revisa el estado del film de tu VAT (FEP, nFEP, PFA, ACF) que no este destensado o dañado
Recuerda SIEMPRE en estos casos revisar que tu cubeta o VAT de resina no tenga restos de resina en el que puedan dañar tu impresora.
Puedes utilizar una espátula o, si tu pantalla cuenta con ello, la opción de limpieza de VAT o test de pantalla para poder retirar una capa fina en toda la superficie de una forma sencilla y asegurando que no queda ningún rastro.
Solo se imprimen soportes el resto queda en el film del VAT

Otro fallo muy común es que nuestros objetos puedan quedar en el film del VAT total o parcialmente mientras que las bases y soportes quedan adheridos a nuestra plataforma:

Normalmente este problema se suele dar porque los soportes no son lo suficientemente fuertes como para mantener el objeto anclado.
Existen diferentes cosas a revisar en este caso:
Ajustes en el perfil de la resina:
incrementar el tiempo de exposición en un 10%
reducir la velocidad de retracción y reentrada a 40mm/min o menos
ajustar el delay light-off para nuestra maquina tenéis una calculadora con tiempos aconsejables aquí
Ajustar las opciones de soportes en tu laminador:
incrementar la densidad de soportes y el diametro de punta
evitar poner soportes en superficies planas, rotar el modelo para evitarlo
evitar los angulos de colocación del modelo que pueda generar deformacion por la tensión del FEP y asegurarse de ahuecar las piezas siempre que sea posible y ser generoso y ubicar correctamente los agujeros de drenaje
para el ahuecado asegúrate que no uses menos de 1.5mm, para impresiones grandes al menos 2mm, y tengamos al menos 2 agujeros de drenaje de 3mm en la parte inferior de la pieza
Impresion de lineas o huecos verticales en todo el eje Z

Si vemos que nuestras impresoras salen con unas lineas o columnas verticales o con agujeros en toda la pieza sobre el eje Z.
Verificar la pantalla, retiraremos el VAT y plataforma de impresión y lanzaremos un test de pantalla que normalmente llevan las impresoras. En el caso que no disponga, con el VAT y la plataforma retirada protegiendo la pantalla con un folio, lanzaremos una impresion de test. Revisaremos que la imagen se muestre correctamente. Si vemos que la imagen en pantalla no es la correcta revisaremos que no sea un problema de un pixel muerto en nuestra pantalla (dejaría una linea o columna de resina en nuestras impresiones) o restos de resina (dejaría huecos en nuestras piezas). En el primer caso, pixel muerto, lo ideal es cambiar la pantalla o intentar no utilizar esa zona para imprimir. Para el caso de tener restos de resina en la pantalla revisaremos posibles filtraciones del VAT y retiraremos, con extremo cuidado, los restos de resina en esta aplicando un poco de IPA unos segundos y retirarndo con un trapo de microfibras... también podemos ayudarnos con un cutter plástico de vitrocerámica con extremo cuidado. También se puede dar el caso de fallos puntuales de la pantalla dejando zonas de la impresion con una zona curada y otras sin, en estos casos revisaremos el estado de la pantalla y de sus conexiones.
Verificar el USB, es aconsejable no utilizar los USB que suelen venir con las impresoras pero independientemente de esto si tenemos el fallo descrito intentaremos usar otro USB. Recuerda que normalmente las impresoras soportan USB en formato FAT32 con particiones de entre 8-16GB y USB 2.0.
Verificar el laminado, en ocasiones podemos ver huecos o columnas de resina, o incluso una fina capa que cubre toda o parcialmente la superficie de impresion, en las impresiones relacionadas con un mal laminado y que pueden ser en partes aleatorias dependiendo de la figura. Podemos realizar la prueba de pantalla como explicamos antes con el objeto que fallen o utilizar el analizador UVtools.
Lineas horizontales en nuestras piezas

En ocasiones se producen unas lineas totalmente horizontales en nuestras impresiones que pueden deber su origen a:
un problema mecánico por desgaste o falta de mantenimiento del eje Z, normalmente suelen aparecer con un patrón y en las mismas alturas
problemas de cambios de temperatura bruscos durante la impresión pueden hacer aparecer líneas o franjas en nuestras piezas, como por ejemplo abrir la cúpula o hacer un pausado de la impresión.
el estado del film puede también afectar en que en determinadas zonas con lineas o franjas horizontales en nuestras impresiones
Las piezas se adhieren demasiado a la plataforma

Aunque no lo consideramos como algo realmente malo en ocasiones una adherencia a la plataforma de impresión muy severa puede hacer que dañemos esta o la figura al retirarla.
una forma de mitigar que dañemos las piezas es no retirarlas de la plataforma hasta realizar el curado. Realizaremos el pre-lavado/lavados de la pieza con estas en la plataforma, eliminaremos los soportes con la ayuda de un secador en la propia plataforma, y una vez retiradas las piezas curaremos y tendremos menos oportunidades de dañar nuestras piezas al retirar los restos de base y soportes nos podemos ayudar del secador para hacer que la tarea sea más sencilla y una espátula o cutter plastico.
podemos de ir ajustando nuestra exposición de capas base reduciendo 5s en cada test para encontrar un balance entre baja (no se adhieren las piezas) o alta adherencia (cuesta retirar las piezas).
Para mas referencia de problemas https://ameralabs.com/blog/resin-3d-printing-troubleshooting-a-comprehensive-guide/
Post-Procesado
Uno de los pasos más importantes de la impresión en resina es el post-procesado que tendremos que aplicar a nuestras impresiones una vez finalizada la impresión.
Es un punto crítico ya que realizarlo de la forma correcta afectará directamente a la calidad final de nuestra impresión además de ser un punto crítico en cuanto a la seguridad al tener que manipular la resina y otros componentes de forma casi directa. Por eso aconsejamos, siguiendo lo recomendado en puntos anteriores:
el uso de guantes, mascarilla y gafas de protección
realizar el proceso en una zona bien ventilada
mantener escrupulosamente la limpieza y orden del área de trabajo y que esta esté en una zona segura alejada de menores o animales
Aunque cada uno suele aplicar el post-procesado de forma diferentes os sugerimos los siguientes pasos:
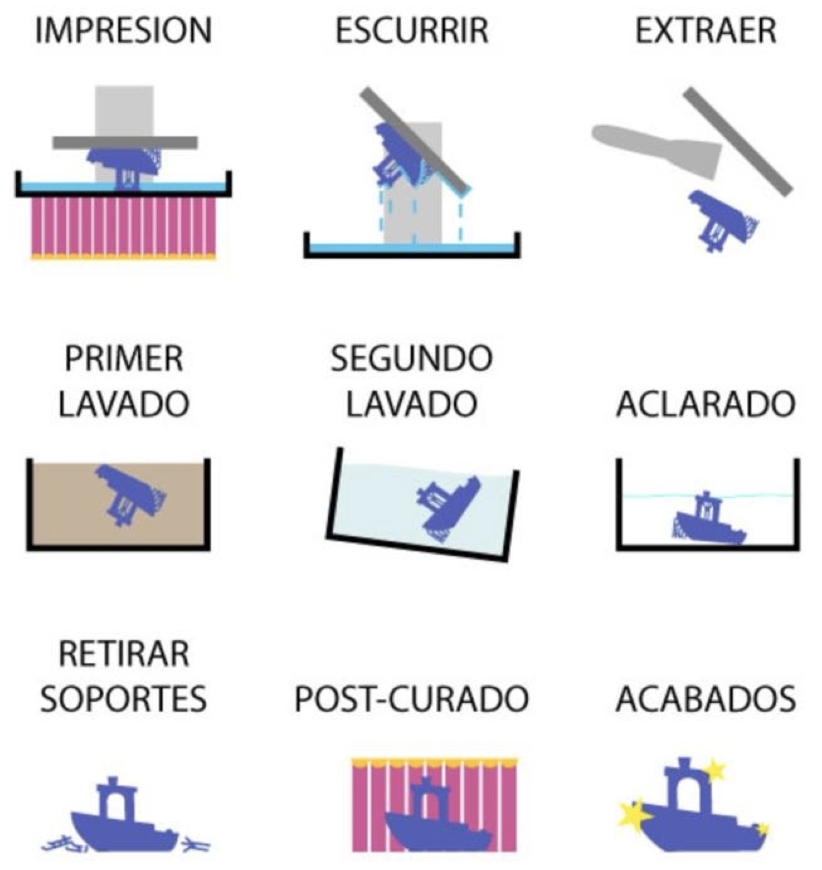
Al finalizar la impresión nos aseguraremos que tenemos todos los componentes y entorno de seguridad listo antes de comenzar el post-procesado
Aunque a continuación os haremos una descripción de los pasos os aconsejamos ver el siguiente video donde tenéis todo el proceso
Escurrido
Teniendo en cuenta el precio de la resina es alto es aconsejable dejar la pieza escurriendo durante unos minutos, además de ahorrar algo en resina también nos facilitará los pasos siguientes.
En plataformas como Thingiverse disponéis de soportes con diferentes ángulos para casi todas las impresoras para poder realizar este paso, podéis encontrar ejemplos en nuestras colecciones de Printables de las principales marcas de impresora junto con otros mods interesantes:

Extracción
Dependiendo del tamaño podemos proceder a la extracción de la pieza/s de la plataforma de impresión, aunque si por comodidad os va mejor realizar los siguientes pasos en ella no debería de ser problema.
Pre-lavado
Idealmente es aconsejable realizar un primer pre-lavado en IPA, probablemente usando reciclado, en el cual retiraremos los restos mayores de resina que puedan quedar sobre la propia pieza y evitando que estos se trasladen al siguiente paso. Este paso lo podemos realizar con un pulverizador sobre una cubeta o en nuestra máquina de limpieza/curado si disponemos de dos recipientes.
Lavado
En este caso si que es aconsejable que usemos IPA en las mejores condiciones. Por la facilidad y mejores resultados se aconseja que se realice en una máquina de limpieza/curado. El tiempo de lavado dependerá del tamaño, detalle, complejidad, tipo de resina y estado de nuestro IPA.
Os recordamos que si utilizamos resina lavable al agua no significa que limpiemos nuetras piezas en el grifo, el agua usada para la limpieza ha de ser tratada después.
Podemos dejar el agua para usarla varias veces, dejarla al son para que se evapore y tirar en un punto limpio los restos o directamente llevarla a un punto limpio.
Jamás debemos tirar el agua con restos de resina por el desagüe!!!
Aclarado
Uno de los pasos más importantes donde, usando agua tibia o aire caliente , aclararemos cualquier resto de resina y podemos usar un cepillo de dientes o similar de cerda blanda para mejorar este aclarado.
Es importante que el aclarado lo hagamos, si lo hacemos con agua tibia/caliente, y que la pieza este unos segundos en ella ya que la calidad final relacionada con el paso posterior dependerán de ello.
Es interesante con un soplador de aire comprimido o un secador en modo frío o incluso con un papel de cocina intentar retirar todos los restos de agua que puedan quedar.
Os aconsejamos el utilizar aire caliente para este proceso, por las siguientes razones:
tal como comentamos en el punto anterior si aclaramos con agua debemos gestionar estos residuos correctamente
el aire permite aclarado además de un secado de los residuos evitando normalmente restos de marcas más tarde
el aire caliente nos permite también reblandecer la resina ligeramente que nos ayudará en el siguiente punto
Retirar soportes
Normalmente todas nuestras impresiones de resina van a necesitar soportes y es en este paso donde los retiraremos usando un cutter o alicates de corte finos. El paso anterior junto con un buen trabajo en el laminador a la hora de poner los soportes marcará la calidad final de nuestra pieza. El uso de agua caliente o aire caliente, aconsejamos esto último, facilita la tarea de retirar soportes dejando menos marcas normalmente.
Curado
Ahora que ya tenemos la pieza completamente limpia y sin soportes procederemos al curado de la resina en nuestra maquina de curado. El tiempo de curado depende de muchas variables como pueden ser el tipo de resina, el tamaño/detalle de la pieza o el tipo/potencia de la máquina de curado.
Como referencia usar un palillo de madera para intentar rascar suavemente la superficie de la pieza, en una parte no visible, nos ayudará a ver si nuestra pieza está o no curada.
Una vez nuestra pieza está curada ya es totalmente seguro poder tocarla.
Acabado transparente resina
Algunas de nuestras impresiones nos puede interesar que, usando resina transparente, queden totalmente transparentes, os damos algunos tips:
Escurriremos a conciencia la resina antes de sacar de la impresora
Realizaremos un pre-lavado y lavado dejando secar la pieza por completo
NO curaremos la pieza bajo UV
Aplicaremos 2 o 3 capas de barniz transparente, es muy aconsejable que este sea anti UV, por todas las caras de la pieza hasta que tenga el acabado deseado
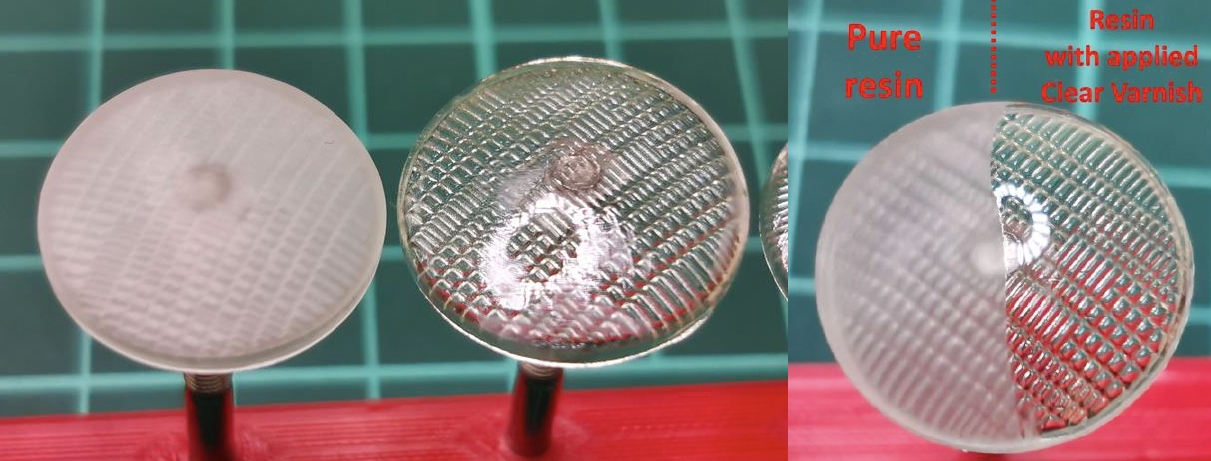
Mantenimiento impresoras de resina
Las impresoras de resina son significativamente más simples y sencillas que otras tecnologías de impresión 3D como SLS o FDM/Filamento. En cualquier caso va a requerir un mantenimiento de las partes mecánicas, electrónica y componentes ópticos.
Consejos generales:
Usa poca cantidad de lubricante: un exceso puede ser contraproducente y atraer más polvo o residuos de resina.
Limpia el exceso: elimina cualquier sobrante para evitar goteos o acumulación de suciedad.
Ten en cuenta el tipo de lubricante: Asegúrate de que sea compatible con los materiales de tu impresora.
Consulta el manual: el manual del fabricante puede tener recomendaciones específicas sobre mantenimiento y lubricación.
Revisión del film del VAT, el film que tenemos en el VAT suele degradarse o dañarse si tenemos fallos en nuestras impresiones. Es importante diferenciar ambos casos:
revisión por fallos de impresión, aunque ya lo hemos comentado siempre se aconseja antes de cada impresión realizar una revisión con una espátula de silicona que no han quedado residuos de una impresión anterior. Más que aconsejable es hacer el proceso anterior cuando nuestra impresión ha fallado parcial o totalmente e incluso hacer una limpieza de tanque, que os explicamos en secciones anteriores, que básicamente va a curar una fina capa de resina que podremos retirar de forma sencilla y nos aseguraremos que no queda nada que pueda estropearnos o perforar el film. Dependiendo del fallo o si vemos filtraciones de resina fuera del tanque es necesario vaciar el VAT de resina y reviar, y cambiar si es necesario ante el mínimo artefacto que veamos.
revisión por uso, los fabricantes suelen sugerir el cambio cada 10K capas impresas si utilizamos como film FEP/nFEP... si usamos ACF serán 30K... aunque estos números son orientativos, dependen de cada fabricante o modelo de máquina. En nuestro caso os sugerimos revisar visualmente el film cuando lleguemos a esos números revisando el correcto tensado del film, algo que deberiamos hacer incluso al llegarnos nueva, o también realizar esta verificación de tensado cada vez que cambiemos de resina al vaciar el VAT de esta.
lubricado del film, aplicar una finísima capa de lubricante PTFE puede mejorar la adherencia de las piezas a la plataforma reduciendo la adherencia del film... especialmente útil en máquinas con gran volumen de impresion o con films con alta flexibilidad. Idealmente realizar el proceso cuando realicemos cambios de resina o cuando notemos que la adherencia, normalmente por el ruído generado durante la impresión al despegar cada capa del film, comience a ser mayor de lo normal.
Revisión de la plataforma de impresión, es aconsejable de forma periódica y coincidiendo con un vaciado del VAT por ejemplo revisar con una regla el estado de la base de impresión que no tengamos problemas de combados y al realizar la nivelación aprovechar para una limpieza a fondo de esta en especial en los tornillos de ajuste/nivelado.
Revisión tanque de resina, suele ser un componente que no prestamos mucha atención pero muy importante para la impresora. Lo ideal es de forma periódica o por ejemplo al cambiar el film realizar un lubricado de los tornillos del tanque así como aplicar lubricante PTFE a las partes metálicas internas y externas de este... esto evitará que los tornillos se puedan atascar con restos de resina o que la resina se adhiera y dañe el tratamiento de la estructura del tanque.
Revisión mecánica, mantener la cinemática/mecánica de tu impresora es imprescindible para obtener los mejores resultados en tus impresoras además de permitir extender la vida útil de esta. Normalmente se aconseja realizar este mantenimiento de forma mensual o cada 100h de uso o al detectar signos de falta de lubricante, rigidez o ruídos en movimientos. Es aconsejable cada vez que vaciemos nuestro VAT de resina aprovechar para limpiar y lubricar las varillas, guías y railes del eje Z, además os aconsejamos repasar los tornillos de anclaje de la columna del eje Z así como limpiar con cuidado el sensor de final de carrera. El proceso de limpieza es muy sencillo:
Con la impresora encendida moveremos la plataforma a 2/3 de su altura máxima
Con un papel de cocina en seco limpiaremos la varilla y las guías lineales, el uso de un liquido/spray limpiador de frenos de automoción suele ir muy bien para una limpieza perfecta.
Con un microfibras aplicaremos el lubricante en la varilla , si preferimos aplicar directamente os aconsejamos utilizar el tubo aplicador que suelen llevar los lubricantes y un papel de cocina para evitar salpicar
Lubricantes aconsejables:
WD-40 Specialist Dry Lube PTFE o similar, en general utilizar lubricantes PTFE en las varillas reduce la friccion y protege esta sin residuos. Este lubricante es aconsejable solamente para la varilla.
Grasa de litio blanca también suele ser aconsejable para el lubricado de varilla/husillo aunque esta suele atraer más la suciedad.
En la guia lineal es mejor utilizar lubricante en grasa de baja viscosisdad que aplicaremos de igual forma que lo anterior comentado anteriormente
Los lubricantes aconsejables son:
Super Lube Synthetic Oil con PTFE o similar, es aconsejable para el uso con las guías lineales también.
Grasa de litio blanca, dada su baja viscosidad es lo aconsejable para las guias lineales y patines
Revisión ventiladores, la impresión en resina genera mucho calor el cual si no tenemos cuidado puede degradar e incluso afectar al funcionamiento de la impresora. Nuestras impresoras cuentan con ventiladores que han de revisarse de forma periódica utilizando un aspirador (para evitar qeu cualquier resto de povo entre en la parte óptica de la impresora. En el caso que tengamos mucha suciedad o ruidos extraños proveniente de los ventiladores lo ideal es desmontar la impresora, con extremo cuidado, y hacer una limpieza y lubricado a fondo de los ventiladores y limpieza interna general.
Revisión LCD y protectores, de nuevo aprovechando un vaciado del VAT es aconsejable realizar una revisión del estado de la pantalla y su protector tanto de forma visual como mediante un test de pantalla.
Nivelación de impresora, nuestras impresoras utilizan resinas en estado liquido y por lo tante es muy importante que esta se encuentre completamente nivelada. Algunas impresoras cuentan con patas o soportes ajustables en altura, en el caso que no tenga es aconsejable montar un sistema ya sea en la impresora o en la superficie donde descanse que nos lo permita, que junto con un nivel (podemos utilizar aplicaciones para móviles de brujula/nivel) nos van a permitir nivelar correctamente. Normalmente este proceso es necesario realizarlo en la puesta en marcha, si modificamos algo de la superficie donde descanse la impresora o su ajuste de las patas.
Última actualización